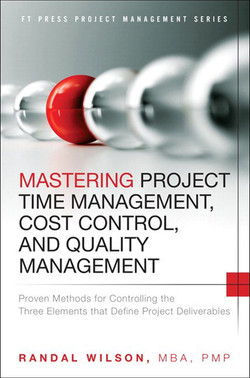
You don't matter whether you're in business for big or small profits, you need to learn how to create and implement a communication plan that works. It is a skill in itself to manage a communication strategy. It is important that you have a communication plan ready to go when you start a new project or redesign. Having an effective communication strategy in place will ensure your business grows without risk.
While you're at the same time, consider how your communications budget will be managed. A budget should allow you to make the most of opportunities, avoid pitfalls, meet your financial obligations, and take advantage of them. The budget you select should be high enough to ensure the growth of your business without compromising your financial well being.
Developing a good communication plan involves using the right mix of media, tactics and time. The key to a good communication plan is to understand your target audience and identify areas where you can improve upon what you already do. It is important to consider the right people and tools in order to ensure that information flows smoothly. It's important to monitor the effectiveness of your communication strategies and make adjustments if necessary.
A discussion with key stakeholders is the best way of determining what works well. For example, you may want to consult a consultant about what types of communication tools will work best for you and your team. This can be done by asking your key employees what types of communication tools they prefer and why. Make sure you incorporate their suggestions into your communication plan. Additionally, it is important to use best practices when creating a communications plan to avoid major missteps.
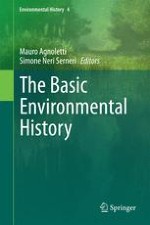
A well-planned and tested communication program is the best. To help you focus your efforts, it is a good idea to include top communication priorities in your budget. As mentioned, it's a smart idea to assess the cost of implementing specific actions in order to get the most value for your dollar. A communication budget that can be easily adjusted to meet the needs of your business is a good idea, especially for those who are planning to expand.
FAQ
What is the main difference between Six Sigma Six Sigma TQM and Six Sigma Six Sigma?
The major difference between the two tools for quality management is that six Sigma focuses on eliminating defect while total quality control (TQM), on improving processes and decreasing costs.
Six Sigma is a method for continuous improvement. It emphasizes the elimination or minimization of defects through statistical methods such control charts and p charts.
This method has the goal to reduce variation of product output. This is achieved by identifying and addressing the root causes of problems.
Total quality management involves measuring and monitoring all aspects of the organization. This includes training employees to improve their performance.
It is often used to increase productivity.
What do we mean when we say "project management"?
It refers to the management of activities related to a project.
Our services include the definition of the scope, identifying requirements, preparing a budget, organizing project teams, scheduling work, monitoring progress and evaluating the results before closing the project.
What is TQM exactly?
The quality movement was born during the industrial revolution when manufacturing companies realized they could not compete on price alone. They needed to improve the quality and efficiency of their products if they were to be competitive.
Management realized the need to improve and created Total Quality Management, which focused on improving all aspects within an organization's performance. It included continuous improvement processes, employee involvement, and customer satisfaction.
What is a simple management tool that aids in decision-making and decision making?
A decision matrix can be a simple, but effective tool to assist managers in making decisions. It helps them to think strategically about all options.
A decision matrix is a way to organize alternatives into rows and columns. This makes it easy for you to see how each option affects other options.
We have four options in this example. They are represented by the boxes to the left of the matrix. Each box represents an option. The top row depicts the current status quo, while the bottom row represents what would happen if no action was taken.
The middle column shows the effect of choosing Option 1. It would increase sales by $2 million to 3 million in this instance.
The results of choosing Option 2 and 3 can be seen in the columns below. These are good changes, they increase sales by $1million or $500,000. These positive changes have their downsides. Option 2, for example, increases the cost by $100 000 while Option 3 decreases profits by $200 000.
The last column displays the results of selecting Option 4. This means that sales will decrease by $1 million.
The best thing about using a decision matrix is that you don't need to remember which numbers go where. You can just glance at the cells and see immediately if one given choice is better.
This is because the matrix has done all the hard work. Simply compare the numbers within the cells.
Here's an example of how you might use a decision matrix in your business.
It is up to you to decide whether to spend more money on advertising. This will allow you to increase your revenue by $5000 per month. However, this will mean that you'll have additional expenses of $10,000.
By looking at the cell just below "Advertising", the net result can be calculated as $15 thousand. Advertising is worth much more than the investment cost.
What are the key management skills?
Management skills are essential for any business owner, whether they're running a small local store or an international corporation. These skills include the ability of managing people, finances, time, space, and other factors.
When you need to manage people, set goals, lead teams, motivate them, solve problems, develop policies and procedures and manage change, management skills are essential.
As you can see there is no end to the number of managerial tasks.
Statistics
- The BLS says that financial services jobs like banking are expected to grow 4% by 2030, about as fast as the national average. (wgu.edu)
- This field is expected to grow about 7% by 2028, a bit faster than the national average for job growth. (wgu.edu)
- Our program is 100% engineered for your success. (online.uc.edu)
- 100% of the courses are offered online, and no campus visits are required — a big time-saver for you. (online.uc.edu)
- Your choice in Step 5 may very likely be the same or similar to the alternative you placed at the top of your list at the end of Step 4. (umassd.edu)
External Links
How To
How do I do the Kaizen Method?
Kaizen means continuous improvement. This term was first used by Toyota Motor Corporation in the 1950s. It refers to the Japanese philosophy that emphasizes continuous improvement through small incremental changes. It's a process where people work together to improve their processes continuously.
Kaizen is one of the most effective methods used in Lean Manufacturing. Employees responsible for the production line should identify potential problems in the manufacturing process and work together to resolve them. This is how you can improve the quality and lower the cost.
The main idea behind kaizen is to make every worker aware of what happens around him/her. If something is wrong, it should be corrected immediately so that no problem occurs. If someone is aware of a problem at work, he/she should inform his/her manager immediately.
When doing kaizen, there are some principles we must follow. Start with the end product, and then move to the beginning. For example, if we want to improve our factory, we first fix the machines that produce the final product. Next, we repair the machines that make components. Then, the machines that make raw materials. Finally, we repair the workers who are directly involved with these machines.
This approach is called 'kaizen' because it focuses on improving everything steps by step. After we're done with the factory, it's time to go back and fix the problem.
It is important to understand how to measure the effectiveness and implementation of kaizen in your company. There are several ways that you can tell if your kaizen system is working. Another way to determine if kaizen is working well is to look at the quality of the products. Another way is to see how much productivity has increased since implementing kaizen.
You can also find out if kaizen works by asking yourself why you decided to implement it. You were trying to save money or obey the law? Did you really believe it would lead to success?
Congratulations if you answered "yes" to any of the questions. You're ready to start kaizen.