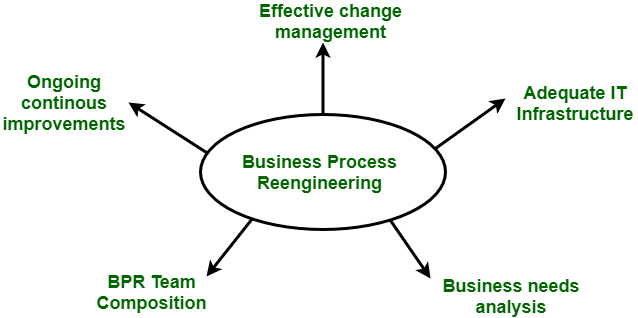
You can learn more about the latest trends and how they will impact your business through supply chain webinars. Many are free and open to the public. Learn more about Supply Chain Management, AI and Machine Learning. Some even touch on Industry 4.0 technologies and Multiparty control towers. These free events are great for business leaders or anyone just interested in learning more about supply chain technology.
Machine Learning
Machine Learning can be used in many ways throughout your supply chain. Machine learning can, for example, optimize factory schedules. It can balance build-to–order and made–to-stock workflows. And it can prevent material delays during production. Machine learning can also detect fraud. It analyses real-time data, looking for patterns and anomalies. Supply chain managers are notified of any problems.
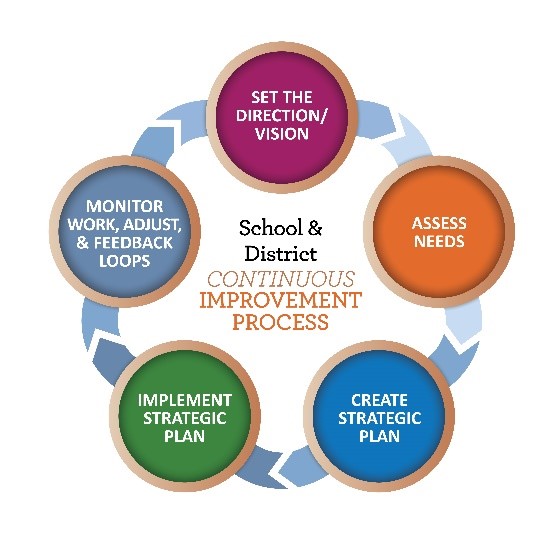
AI
Supply chains can benefit from predictive analytics. Interpreting the data generated with this technology can prove difficult. This webinar will help supply chain executives understand the basics and how AI can be applied to their business.
Industry 4.0 technologies
The Digital Supply Chain, or Industry 4.0, represents a fundamental shift in how businesses conduct business. The speed of change makes it challenging to distill the competitive advantage from the new technologies. This Capstone Webinar will provide an overview of the key domains and agents that are driving transformation. The webinar will also answer some of the most frequent questions about key technology.
Multiparty control towers
Multiparty control rooms are an important component of the supply chain and offer many benefits for companies. They enable companies to automate repetitive tasks and save money and time. Multiparty control centers can be very powerful when used in conjunction to orchestration platforms. These solutions are able to connect all of the different parts of a supply network ecosystem and provide a single source truth for all parties.
Collaboration in the supply chain
Collaboration within the supply chains is becoming a more popular strategy that can have significant benefits for a company's bottom lines. In addition to increasing operational efficiencies, collaborative relationships can also foster greater innovation and risk management. Collaboration can occur in both vertical and horizontal dimensions. However, there are key factors to be aware of.
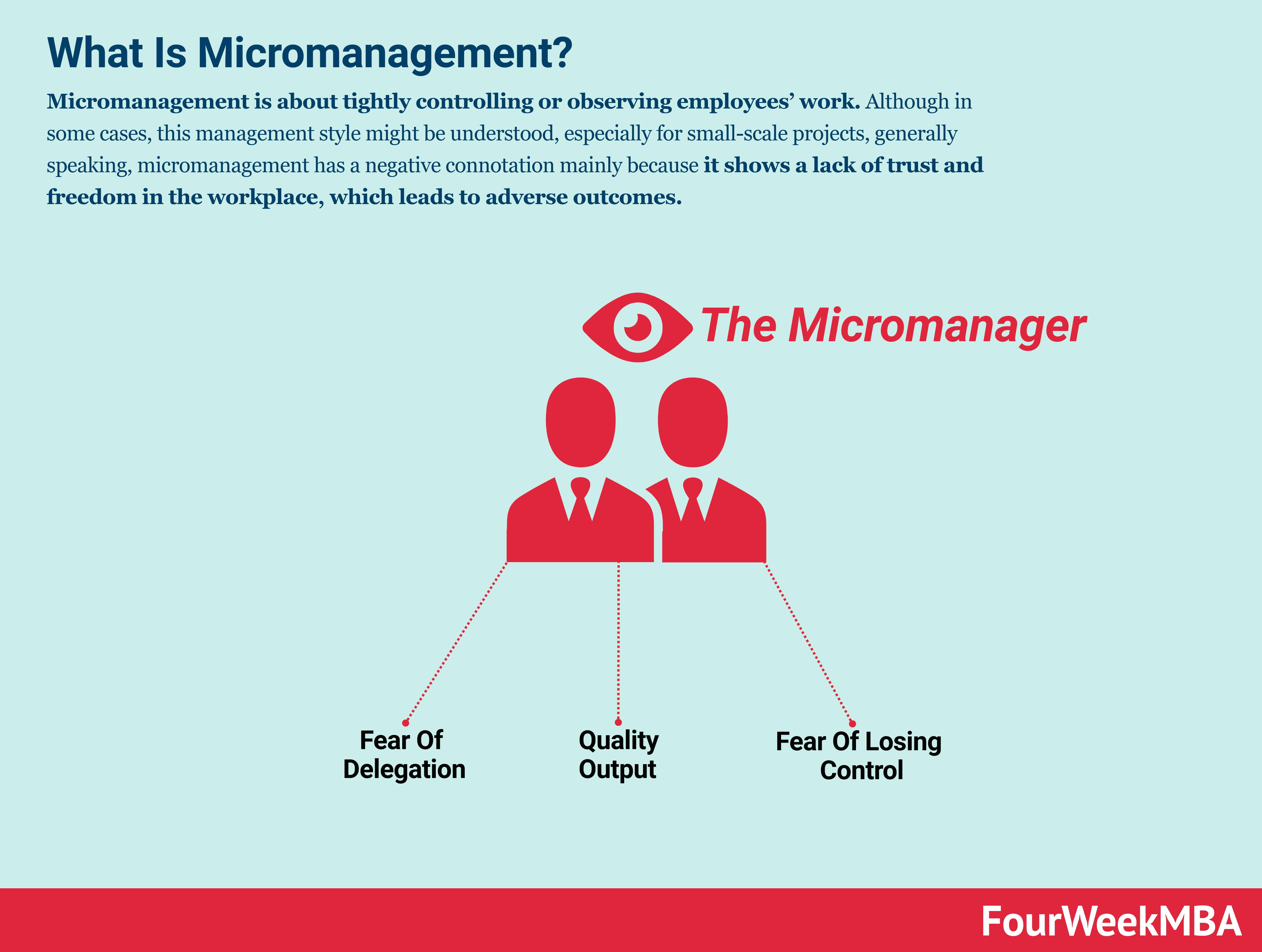
The future of supply chains
Future of the supply chain webinars discuss the challenges facing supply chains. They will discuss how to make them more sustainable, integrate corporate governance in value chains, and improve access for consumers to medicines and medical devices. The speakers also discuss how to deal with the increasing convergence of ESG and antitrust issues. The session will address trends in supply chains beginning in 2022 and beyond.
FAQ
How does Six Sigma work
Six Sigma uses statistical analysis to find problems, measure them, analyze root causes, correct problems, and learn from experience.
The first step to solving the problem is to identify it.
Next, data will be collected and analyzed to determine trends and patterns.
The problem can then be fixed by taking corrective measures.
Finally, data is reanalyzed to determine whether the problem has been eliminated.
This continues until you solve the problem.
How do we build a culture that is successful in our company?
Successful company culture is one where people feel valued and respected.
It's built on three fundamental principles:
-
Everyone has something valuable to contribute
-
People are treated fairly
-
People and groups should respect each other.
These values are reflected by the way people behave. They will treat others with kindness and consideration.
They will listen to other people's opinions respectfully.
These people will inspire others to share thoughts and feelings.
The company culture promotes collaboration and open communication.
People can freely express their opinions without fear or reprisal.
They are aware that mistakes can be accepted if they are treated honestly.
The company culture encourages honesty and integrity.
Everyone is aware that truth must be told.
Everyone is aware that rules and regulations apply to them.
Nobody expects to be treated differently or given favors.
What is the difference between management and leadership?
Leadership is about inspiring others. Management is all about controlling others.
Leaders inspire followers, while managers direct workers.
Leaders motivate people to succeed; managers keep workers on track.
A leader develops people; a manager manages people.
What are the main management skills?
Management skills are essential for any business owner, whether they're running a small local store or an international corporation. They include the ability to manage people, finances, resources, time, and space, as well as other factors.
When you need to manage people, set goals, lead teams, motivate them, solve problems, develop policies and procedures and manage change, management skills are essential.
As you can see, there are many managerial responsibilities!
Statistics
- 100% of the courses are offered online, and no campus visits are required — a big time-saver for you. (online.uc.edu)
- As of 2020, personal bankers or tellers make an average of $32,620 per year, according to the BLS. (wgu.edu)
- The BLS says that financial services jobs like banking are expected to grow 4% by 2030, about as fast as the national average. (wgu.edu)
- This field is expected to grow about 7% by 2028, a bit faster than the national average for job growth. (wgu.edu)
- UpCounsel accepts only the top 5 percent of lawyers on its site. (upcounsel.com)
External Links
How To
How do I get my Six Sigma License?
Six Sigma is an effective quality management tool that can improve processes and increase productivity. It's a system that allows companies to get consistent results from operations. The name is derived from the Greek word "sigmas", which means "six". Motorola invented this process in 1986. Motorola realized that it was important to standardize manufacturing processes so they could produce products quicker and cheaper. The many people involved in manufacturing had caused problems with consistency. They used statistical tools such as Pareto analysis, control charts, and Pareto analysis to resolve the problem. These techniques would be applied to every aspect of the operation. So, after applying this technique, they would be able to make changes where there was room for improvement. When you are trying to obtain your Six Sigma certification, there are three steps. The first step is to find out if you're qualified. Before you can take any tests, you will need to take some classes. You can then start taking the tests once you have completed those classes. The class material will be reviewed. Once you have completed the class, you will be ready for the test. If you pass, you'll get certified. Final, your certifications can be added to you resume.