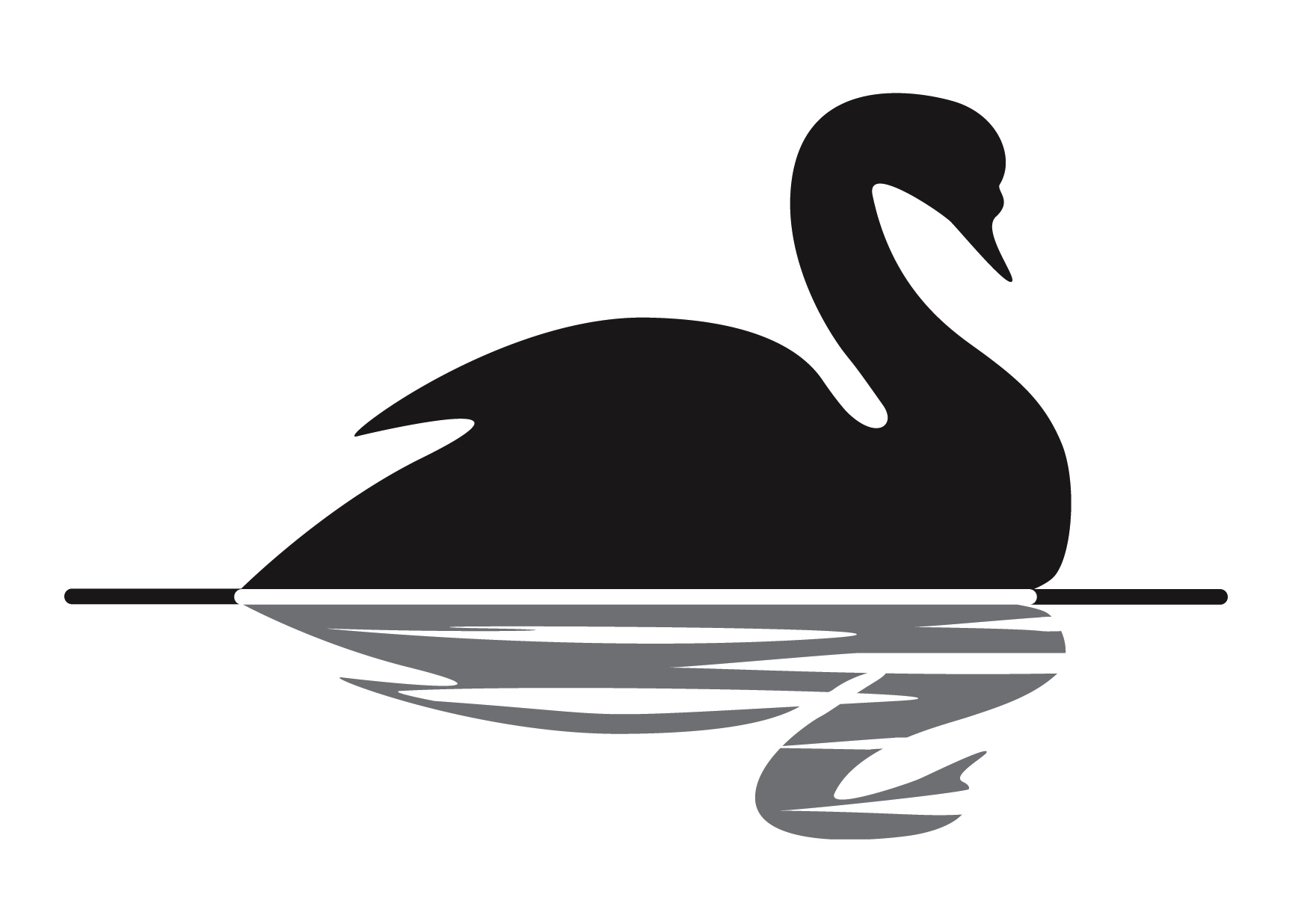
Courses in construction scheduling and planning equip students with the necessary skills to successfully manage construction projects. They teach students how communicate effectively with others, understand the different alternatives, and plan the project's lifespan. Topics include how to plan a construction project's life cycle, the activities that should be included in a work breakdown structure, sequencing, and what information should be included in a schedule. The course covers all phases involved in a construction project: sitework, structure, post-construction, and more.
Prerequisites
Construction Planning and Scheduling is an introduction course that teaches you how to manage and schedule construction projects. It will teach you how to plan and execute construction projects. It is a Gold Seal accredited training program and a CIQS credit course with the Canadian Institute of Quantity Surveyors.
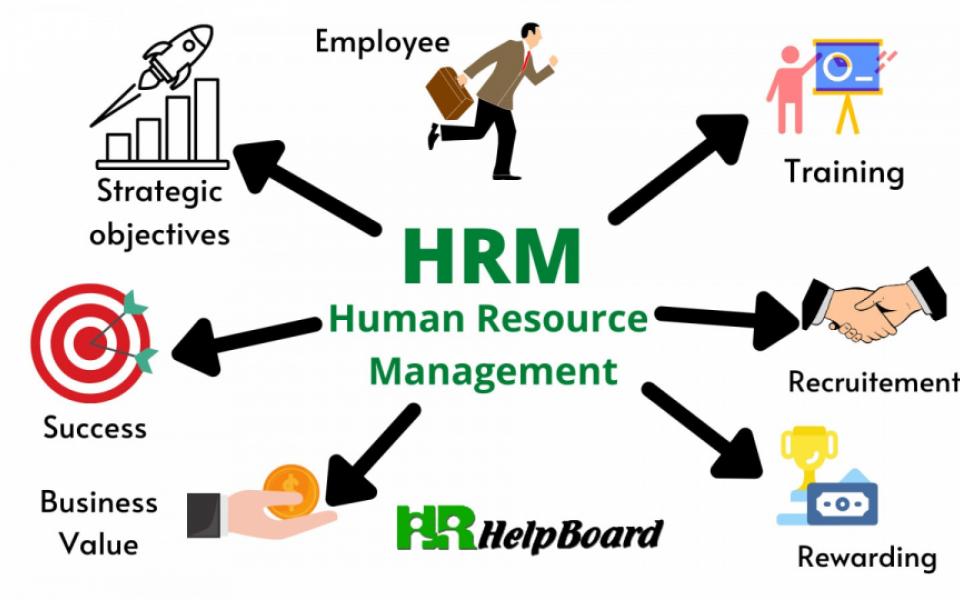
This course introduces construction project planning through the use computer applications, network-based scheduling methods and cost analysis. Also covered are the Gantt program, critical path method and resource allocation. The course also introduces students cash flow planning as well as the schedule controls for construction projects.
Assessment weightings
Computer applications can be used to plan and schedule construction projects. These courses use Gantt charts and bar charts to show the relationships between different construction activities. The course provides students with a quality education and relevant training in construction. It also covers topics such as project cost control and resource levels.
Each assessment must be passed with a minimum of 40%. They also must perform budgeting and cash flow analysis for real-life construction projects. They will also need to analyze project risks using PERT, Monte Carlo, and Critical Path Methods. Earned-Value Management, a systematic approach to cost and project monitoring will be covered by students.
Instructors
Students will learn the basics of construction scheduling and planning. They provide information about project planning methods such as Gantt charts, network scheduling techniques (CPM), critical path method (CPM), and resource leveling. They also teach students how to use construction schedules as well as computer-based planning software.
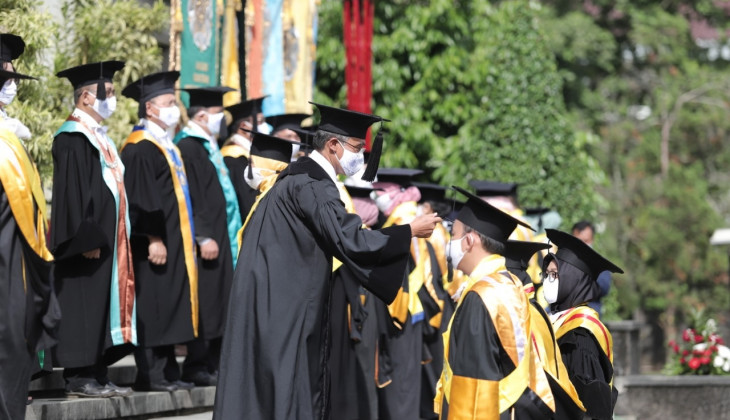
These courses will teach you how to plan, manage and progress a building project. The materials used in the course will include lectures, text, outside speakers, site visits, case studies, and computers.
FAQ
What are some common mistakes managers make when managing people?
Sometimes managers make their job harder than they need to.
They may not assign enough responsibilities to staff members and provide them with inadequate support.
In addition, many managers lack the communication skills required to motivate and lead their teams.
Managers sometimes set unrealistic expectations of their teams.
Some managers may try to solve every problem themselves instead of delegating responsibility to others.
What does Six Sigma mean?
Six Sigma uses statistical analysis for problems to be found, measured, analyzed root causes, corrected, and learned from.
The first step is identifying the problem.
The next step is to collect data and analyze it in order to identify trends or patterns.
Then, corrective actions can be taken to resolve the problem.
Finally, data is reanalyzed to determine whether the problem has been eliminated.
This cycle continues until there is a solution.
What is the difference between leadership and management?
Leadership is about inspiring others. Management is about controlling others.
A leader inspires others while a manager directs them.
A leader motivates people and keeps them on task.
A leader develops people; a manager manages people.
What role does a manager have in a company's success?
There are many roles that a manager can play in different industries.
The manager oversees the day-to-day activities of a company.
He/she ensures that the company meets its financial obligations and produces goods or services that customers want.
He/she ensures employees adhere to all regulations and quality standards.
He/she plans new products and services and oversees marketing campaigns.
How do you manage employees effectively?
Effectively managing employees requires that you ensure their happiness and productivity.
It is important to set clear expectations about their behavior and keep track of their performance.
Managers need clear goals to be able to accomplish this.
They need to communicate clearly with staff members. They need to communicate clearly with their staff.
They must also keep track of the activities of their team. These include:
-
What did you accomplish?
-
How much work was put in?
-
Who did it all?
-
What was the moment it was completed?
-
Why?
This information can be used to monitor performance and evaluate results.
Statistics
- 100% of the courses are offered online, and no campus visits are required — a big time-saver for you. (online.uc.edu)
- The profession is expected to grow 7% by 2028, a bit faster than the national average. (wgu.edu)
- The average salary for financial advisors in 2021 is around $60,000 per year, with the top 10% of the profession making more than $111,000 per year. (wgu.edu)
- The BLS says that financial services jobs like banking are expected to grow 4% by 2030, about as fast as the national average. (wgu.edu)
- Hire the top business lawyers and save up to 60% on legal fees (upcounsel.com)
External Links
How To
How does Lean Manufacturing work?
Lean Manufacturing is a method to reduce waste and increase efficiency using structured methods. They were created by Toyota Motor Corporation in Japan in the 1980s. The primary goal was to make products with lower costs and maintain high quality. Lean manufacturing focuses on eliminating unnecessary steps and activities from the production process. It includes five main elements: pull systems (continuous improvement), continuous improvement (just-in-time), kaizen (5S), and continuous change (continuous changes). It is a system that produces only the product the customer requests without additional work. Continuous improvement refers to continuously improving existing processes. Just-in-time refers to when components and materials are delivered directly to the point where they are needed. Kaizen stands for continuous improvement. Kaizen can be described as a process of making small improvements continuously. Last but not least, 5S is for sort. These five elements work together to produce the best results.
The Lean Production System
Six key concepts make up the lean manufacturing system.
-
Flow - focuses on moving information and materials as close to customers as possible.
-
Value stream mapping - break down each stage of a process into discrete tasks and create a flowchart of the entire process;
-
Five S's – Sort, Put In Order Shine, Standardize and Sustain
-
Kanban is a visual system that uses visual cues like stickers, colored tape or stickers to keep track and monitor inventory.
-
Theory of constraints - identify bottlenecks in the process and eliminate them using lean tools like kanban boards;
-
Just-in-time delivery - Deliver components and materials right to your point of use.
-
Continuous improvement is making incremental improvements to your process, rather than trying to overhaul it all at once.