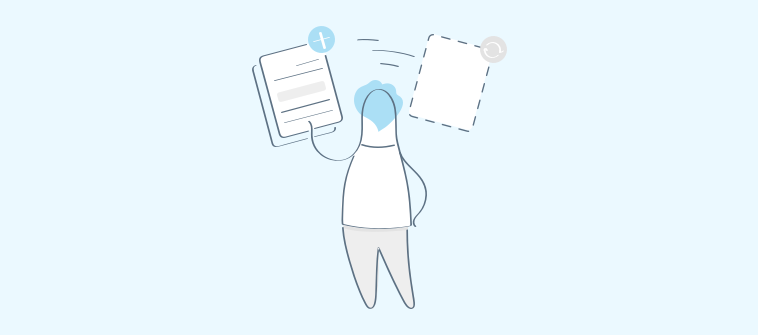
Logistics includes the time taken to complete a supply chain. It is the time that it takes for a product to be shipped and received. This time is also called shipping lead time, handling lead time, or shipping time. This is crucial for meeting customer needs and increasing business productivity. The lead time is also an important factor in inventory management. It helps you understand costs related to different parts of your supply chains. Let's look at some of the most important components of lead time.
Inventory carrying cost
Supply chain metrics such as lead time and inventory cost should be closely monitored. High levels of either one or both can signify that inventory has become overstocked. In this case, you should adjust order frequency to keep stock moving. Because it measures how much inventory a company keeps, carrying cost is important to monitor.
The biggest component of inventory carrying costs is the cost to capital. It covers the capital required to purchase products as well any interest or loan fees. This can negatively impact cash flow, leading to the need for additional capital. Companies can limit these costs by forecasting their demand for goods and making better purchases. They can also negotiate lower purchases with suppliers.
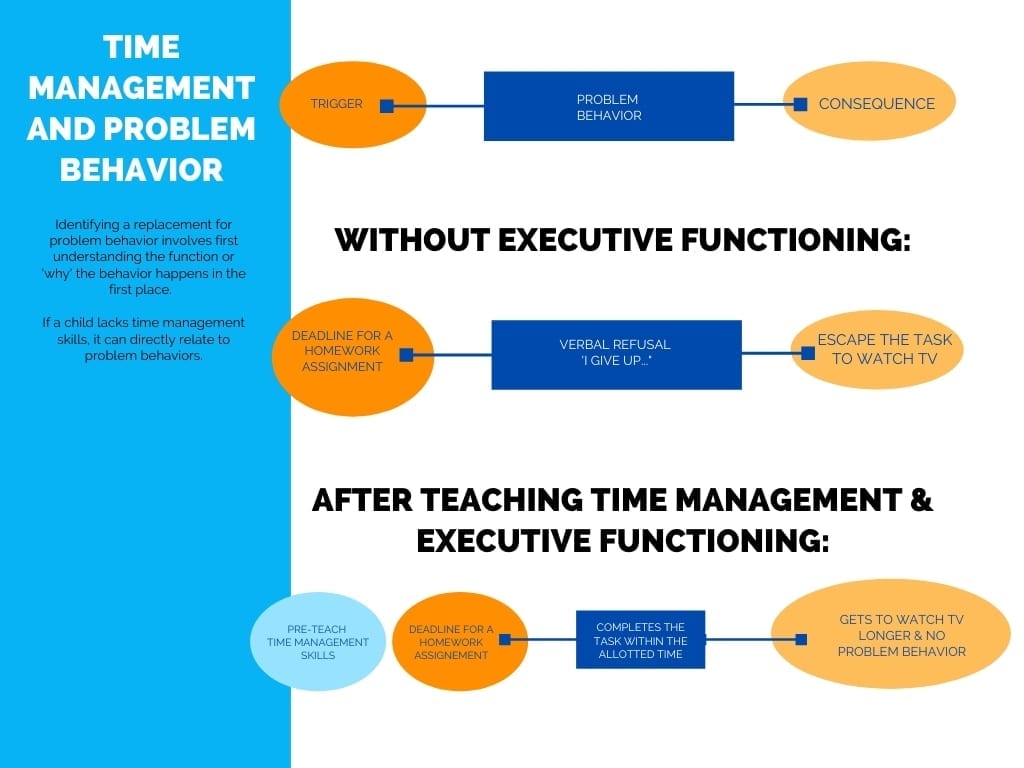
Delivery lead time
The delivery lead time is the time taken between placing an order and receiving it. This must be done for each product in the supply chain. This time can vary depending on how many pieces of the chain are purchased and each piece's production capability. They will have accumulated each player's lead time by the time the customer reaches the end. It is therefore crucial to accurately measure that time.
The first step towards reducing the supply chain's lead times is to identify the crucial parts of the process. If a company has to produce certain quantities of custom water bottles in a short time, they can reduce their lead times by identifying the parts that take longer than one working day. For instance, if the manufacturer has to produce a certain number of water bottles in a day, they can program a printing machine to start the process while the bottles are being manufactured.
Ordering lead time
Improving lead times is crucial in managing a supply channel. This can easily be achieved by improving supplier relationships and streamlining the ordering process. You can also speed up your order-to–delivery time by placing orders sooner and communicating more often with suppliers. This will improve the customer experience and reduce time to receive orders.
Depending on your business, lead times can vary. This is because lead times are dependent on the product and how far in advance you place orders. It also depends upon the supplier you use. If you order something Monday morning, it might take one week for it to reach you. By contrast, if you order it on Friday, it could take four days to receive it. It is important to calculate each component of the supply chains separately in order for you to obtain a more accurate estimate of the lead time.
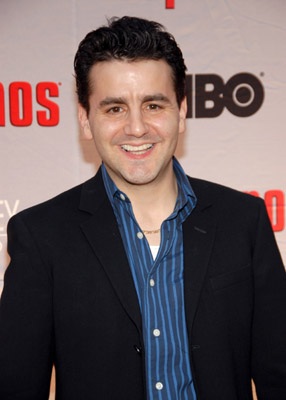
Customer satisfaction
Supply chain management is based on customer satisfaction. When calculating lead-times, companies need to consider the time it takes for items to be procured, produced, and shipped. Many factors can influence lead times. Lead times may be long or short. Supplier lead times may vary from one day to the next, and the exact amount depends on the supplier.
To improve customer satisfaction, businesses should measure their performance on key metrics. It is possible to measure order accuracy and delivery speed as well as replacement time. The supply chain of a company is a key factor in determining how satisfied customers are. Clients can pinpoint problem areas by using analytics that track the progress throughout the supply chain.
FAQ
What is the role of a manager in a company?
Different industries have different roles for managers.
In general, a manager controls the day-to-day operations of a company.
He/she ensures the company meets its financial commitments and produces goods/services that customers demand.
He/she makes sure that employees adhere to the rules and regulations as well as quality standards.
He/she plans and oversees marketing campaigns.
What are management concepts, you ask?
Management Concepts are the principles and practices managers use to manage people and resources. They cover topics such as job descriptions and performance evaluations, human resource policies, training programs, employee motivation, compens systems, organizational structure, among others.
Six Sigma is so popular.
Six Sigma can be implemented quickly and produce impressive results. It provides a framework that allows for improvement and helps companies concentrate on what really matters.
Why is it important for companies to use project management techniques?
Project management techniques ensure that projects run smoothly while meeting deadlines.
This is because most businesses rely heavily on project work to produce goods and services.
These projects require companies to be efficient and effective managers.
Companies that do not manage their projects effectively risk losing time, money, or reputation.
What is TQM exactly?
The industrial revolution was when companies realized that they couldn't compete on price alone. This is what sparked the quality movement. They needed to improve quality and efficiency if they were going to remain competitive.
Management developed Total Quality Management to address the need for improvement. It focused on all aspects of an organisation's performance. It included continuous improvement, employee involvement and customer satisfaction.
Statistics
- Your choice in Step 5 may very likely be the same or similar to the alternative you placed at the top of your list at the end of Step 4. (umassd.edu)
- Hire the top business lawyers and save up to 60% on legal fees (upcounsel.com)
- The BLS says that financial services jobs like banking are expected to grow 4% by 2030, about as fast as the national average. (wgu.edu)
- 100% of the courses are offered online, and no campus visits are required — a big time-saver for you. (online.uc.edu)
- This field is expected to grow about 7% by 2028, a bit faster than the national average for job growth. (wgu.edu)
External Links
How To
How can you implement Quality Management Plan (QMP).
Quality Management Plan (QMP), which was introduced in ISO 9001:2008, provides a systematic approach to improving processes, products, and services through continual improvement. It focuses on the ability to measure, analyze and control processes and customer satisfaction.
The QMP is a standard method used to ensure good business performance. The QMP aims to improve the process of production, service delivery, and customer relationship. QMPs must include all three elements - Products, Services, and Processes. When the QMP includes only one aspect, it is called a "Process" QMP. If the QMP is focused on a product/service, it's called a QMP. QMP is also used to refer to QMPs that focus on customer relations.
Two main elements are required for the implementation of a QMP. They are Scope and Strategy. These elements are as follows:
Scope: This describes the scope and duration for the QMP. For example, if your organization wants to implement a QMP for six months, this scope will define the activities performed during the first six months.
Strategy: These are the steps taken in order to reach the goals listed in the scope.
A typical QMP is composed of five phases: Planning Design, Development, Implementation and Maintenance. The following describes each phase.
Planning: This stage is where the QMP objectives are identified and prioritized. To understand the expectations and requirements of all stakeholders, the project is consulted. After identifying the objectives, priorities and stakeholder involvement, it's time to develop the strategy for achieving the goals.
Design: In this stage, the design team designs the vision and mission, strategies, as well as the tactics that will be required to successfully implement the QMP. These strategies are put into action by developing detailed plans and procedures.
Development: Here, the team develops the resources and capabilities that will support the successful implementation.
Implementation: This refers to the actual implementation or the use of the strategies planned.
Maintenance: This is an ongoing procedure to keep the QMP in good condition over time.
Additional items must be included in QMP.
Stakeholder Engagement: It is crucial for the QMP to be a success. They should actively be involved during the planning and development, implementation, maintenance, and design stages of QMP.
Project Initiation - A clear understanding of the problem statement, and the solution is necessary for any project to be initiated. The initiator must know the reason they are doing something and the expected outcome.
Time Frame: It is important to consider the QMP's time frame. You can use a simplified version if you are only going to be using the QMP for short periods. If you're looking to implement the QMP over a longer period of time, you may need more detailed versions.
Cost Estimation: Another important component of the QMP is cost estimation. You can't plan without knowing how much money it will cost. Therefore, cost estimation is essential before starting the QMP.
QMPs are not just a written document. They should be a living document. It changes as the company grows. It should be reviewed on a regular basis to ensure that it is still meeting the company's needs.