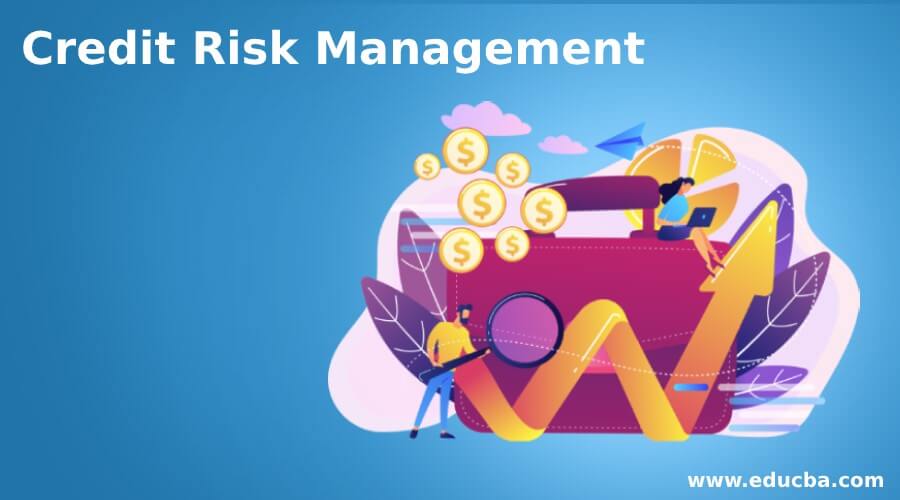
Before you can keep track of hazardous materials and report them to EPA, it is necessary that they be identified. You can also reach out to your state's environmental agencies for information about upcoming rules. These agencies also have information regarding federal hazardous materials regulations. These agencies can also assist you in your hazardous waste management plans.
Tracking hazardous materials
You are likely in hazardous waste management and know how important it can be to track where the waste ends up and how it gets to the landfill. The Resource Conservation and Recovery Act of 1996 was created to deal with the increasing amount of waste in society. The law introduced new regulations that address the growing problem of hazardous waste and require safe disposal. The legislation also contained national goals regarding environmental protection, conservation, health, and human rights. The legislation also created the concept of "cradle - grave" waste management.
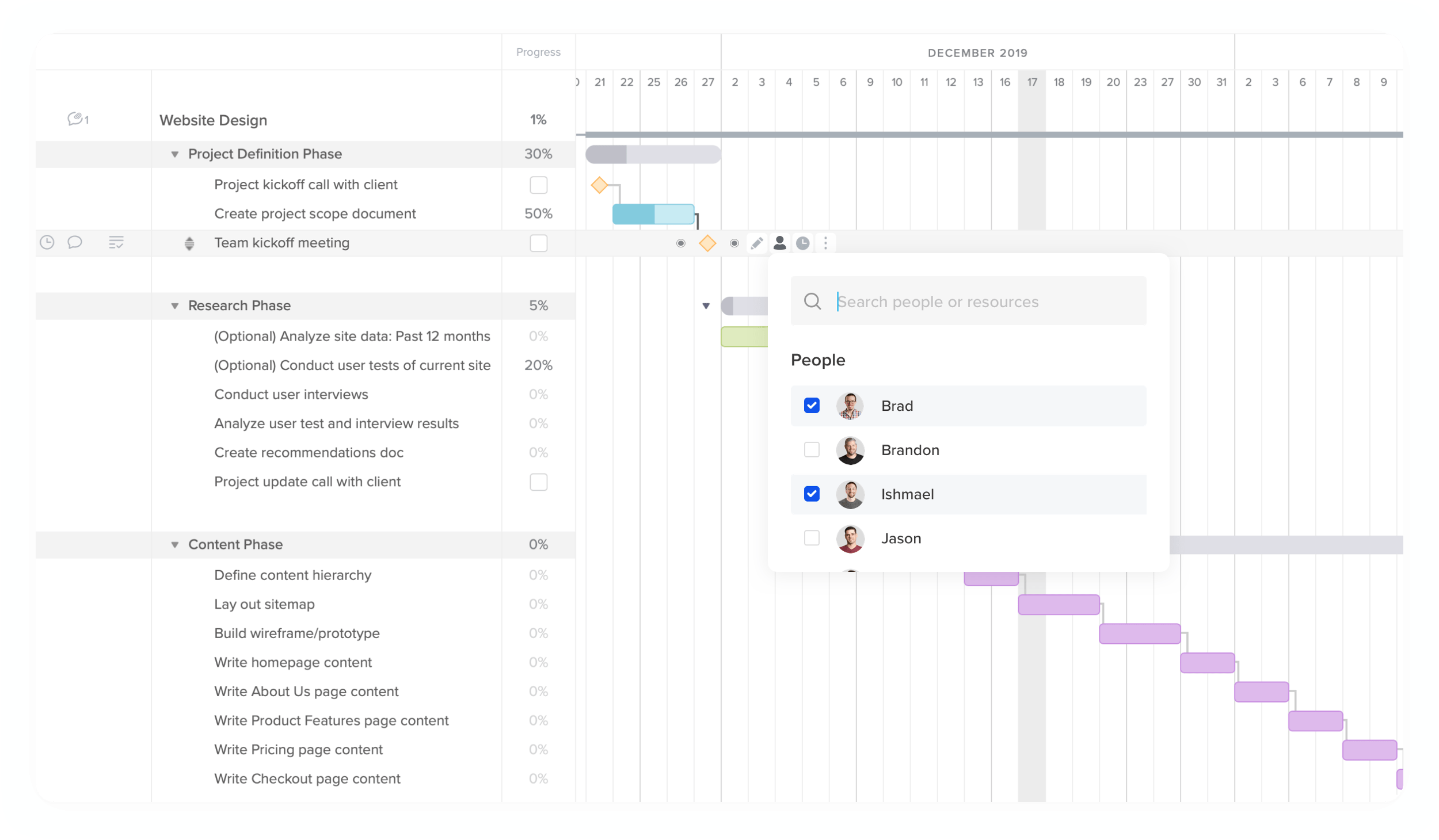
The Resource Guide provides a range of activities to increase students' understanding of hazardous wastes and solid waste issues. These activities can either be added to an existing curriculum or used on their own. The Guide also has a large list of solid-waste resources.
Report hazardous wastes (EPA)
There are many things to consider when reporting hazardous wastes the EPA. The reporting requirements for hazardous wastes vary depending on their type. If your site is contaminated, you might need to report hazardous materials from off-site sources. If you have a public wastewater treatment facility, you may also need to report wastes from offsite sources. You can find information from your state's environmental agency about hazardous waste disposal regulations.
EPA Form 8700-13 will help you identify hazardous wastes that you need to report. You will also find instructions on how you can submit the report online. For large sites, you can submit the WR section outside of the online reporting system. The EPA will send you the specifications for completing your report. Specific waste types may require special reporting, such as asbestos, PCBs, waste oils, and hazardous/radioactive nuclear mixed waste. Foreign wastes may also need reporting.
Manage hazardous wastes
Handling hazardous wastes requires complex coordination between many stakeholders. A waste that is radioactive, flammable or otherwise harmful to the environment must be managed according to comprehensive policies. These policies will outline the roles of all parties and provide incentives for reducing waste quantities. They also include systems to control the movement and disposal hazardous wastes. These policies must be coordinated with other policies and topics to protect the environment and human rights.
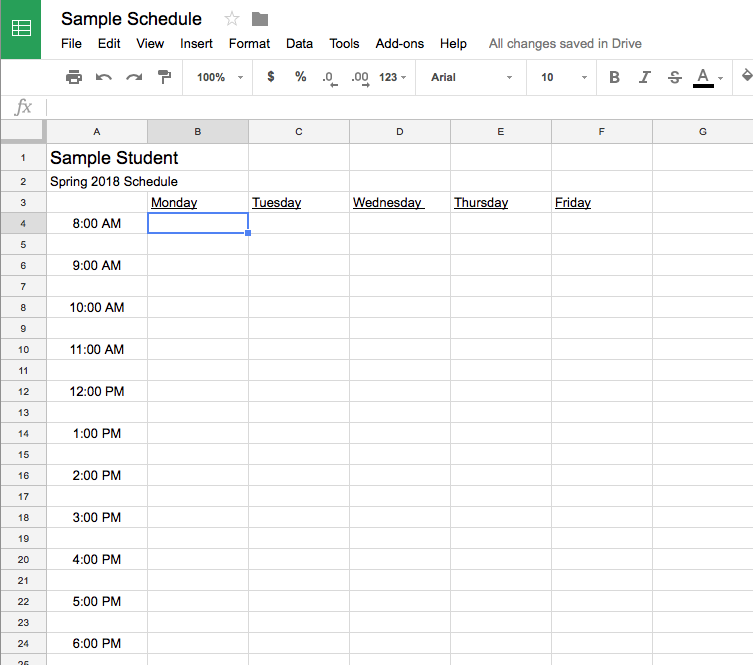
Chemical wastes containing potentially toxic chemicals are often considered to be hazardous. The EPA maintains a P list of dangerous chemicals. These chemicals must be classified as hazardous wastes once they have been disposed of. This includes any containers that contain these chemicals.
FAQ
What is Kaizen, exactly?
Kaizen, a Japanese term that means "continuous improvement," is a philosophy that encourages employees and other workers to continuously improve their work environment.
Kaizen is built on the belief that everyone should be able do their jobs well.
How does a manager motivate their employees?
Motivation refers to the desire or need to succeed.
Enjoyable activities can motivate you.
You can also get motivated by seeing your contribution to the success or the improvement of the organization.
You might find it more rewarding to treat patients than to study medical books if you plan to become a doctor.
Motivation comes from within.
For example, you might have a strong sense of responsibility to help others.
You may even find it enjoyable to work hard.
Ask yourself why you aren't feeling motivated.
Then, consider ways you could improve your motivation.
What does "project management" mean?
Management is the act of managing activities in order to complete a project.
Our services include the definition of the scope, identifying requirements, preparing a budget, organizing project teams, scheduling work, monitoring progress and evaluating the results before closing the project.
What is the main difference between Six Sigma Six Sigma TQM and Six Sigma Six Sigma?
The major difference between the two tools for quality management is that six Sigma focuses on eliminating defect while total quality control (TQM), on improving processes and decreasing costs.
Six Sigma is a methodology for continuous improvement. This method emphasizes eliminating defects using statistical methods such p-charts, control charts, and Pareto analysis.
This method aims to reduce variation in product production. This is achieved by identifying and addressing the root causes of problems.
Total Quality Management involves monitoring and measuring every aspect of the organization. It also involves training employees to improve performance.
It is frequently used as an approach to increasing productivity.
Why is project management so important?
Project management techniques ensure that projects run smoothly while meeting deadlines.
This is because many businesses depend heavily upon project work to produce products and services.
Companies must manage these projects effectively and efficiently.
Without effective project management, companies may lose money, time, and reputation.
What role does a manager have in a company's success?
Different industries have different roles for managers.
The manager oversees the day-to-day activities of a company.
He/she ensures the company meets its financial commitments and produces goods/services that customers demand.
He/she is responsible for ensuring that employees comply with all regulations and follow quality standards.
He/she oversees marketing campaigns and plans new products.
Statistics
- The profession is expected to grow 7% by 2028, a bit faster than the national average. (wgu.edu)
- Hire the top business lawyers and save up to 60% on legal fees (upcounsel.com)
- This field is expected to grow about 7% by 2028, a bit faster than the national average for job growth. (wgu.edu)
- UpCounsel accepts only the top 5 percent of lawyers on its site. (upcounsel.com)
- 100% of the courses are offered online, and no campus visits are required — a big time-saver for you. (online.uc.edu)
External Links
How To
How is Lean Manufacturing done?
Lean Manufacturing is a method to reduce waste and increase efficiency using structured methods. They were created in Japan by Toyota Motor Corporation during the 1980s. The aim was to produce better quality products at lower costs. Lean manufacturing focuses on eliminating unnecessary steps and activities from the production process. It is made up of five elements: continuous improvement, continuous improvement, just in-time, continuous change, and 5S. Pull systems involve producing only what the customer wants without any extra work. Continuous improvement involves constantly improving upon existing processes. Just-in time refers to components and materials being delivered right at the place they are needed. Kaizen refers to continuous improvement. It is achieved through small changes that are made continuously. The 5S acronym stands for sort in order, shine standardize and maintain. These five elements are used together to ensure the best possible results.
Lean Production System
Six key concepts are the basis of lean production:
-
Flow: The goal is to move material and information as close as possible from customers.
-
Value stream mapping- This allows you to break down each step of a process and create a flowchart detailing the entire process.
-
Five S's - Sort, Set In Order, Shine, Standardize, and Sustain;
-
Kanban – visual signals like colored tape, stickers or other visual cues are used to keep track inventory.
-
Theory of constraints: Identify bottlenecks and use lean tools such as kanban boards to eliminate them.
-
Just-intime - Order components and materials at your location right on the spot.
-
Continuous improvement - Make incremental improvements rather than overhauling the entire process.