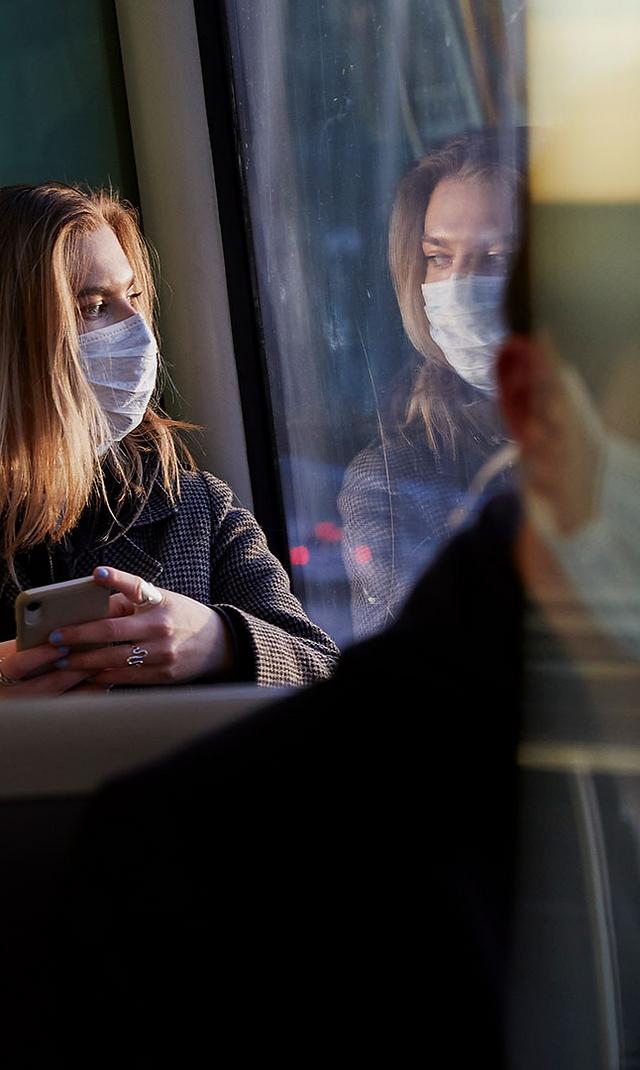
You need to know mathematics in order to manage construction projects. Even basic construction projects like building a concrete wall can require some math. The concrete wall might be 100 feet in length, ten feet tall, and one feet thick. A brick veneer wall is also possible. This would consist of bricks 8 inches long by 3 inches high. This is not an easy task, so you'll need to learn more than basic algebra and geometry to make it work.
Prerequisites for construction management degree
A strong math foundation is essential for students who wish to enter construction management. General contractors and construction firms often hire math- and statistics-savvy graduates. Regularly, government agencies employ graduates. Candidates must also have completed one-year of mathematics in high school. All careers in construction require math. There are many levels in construction management. Students can choose to focus on heavy/civil, general, or a combination.
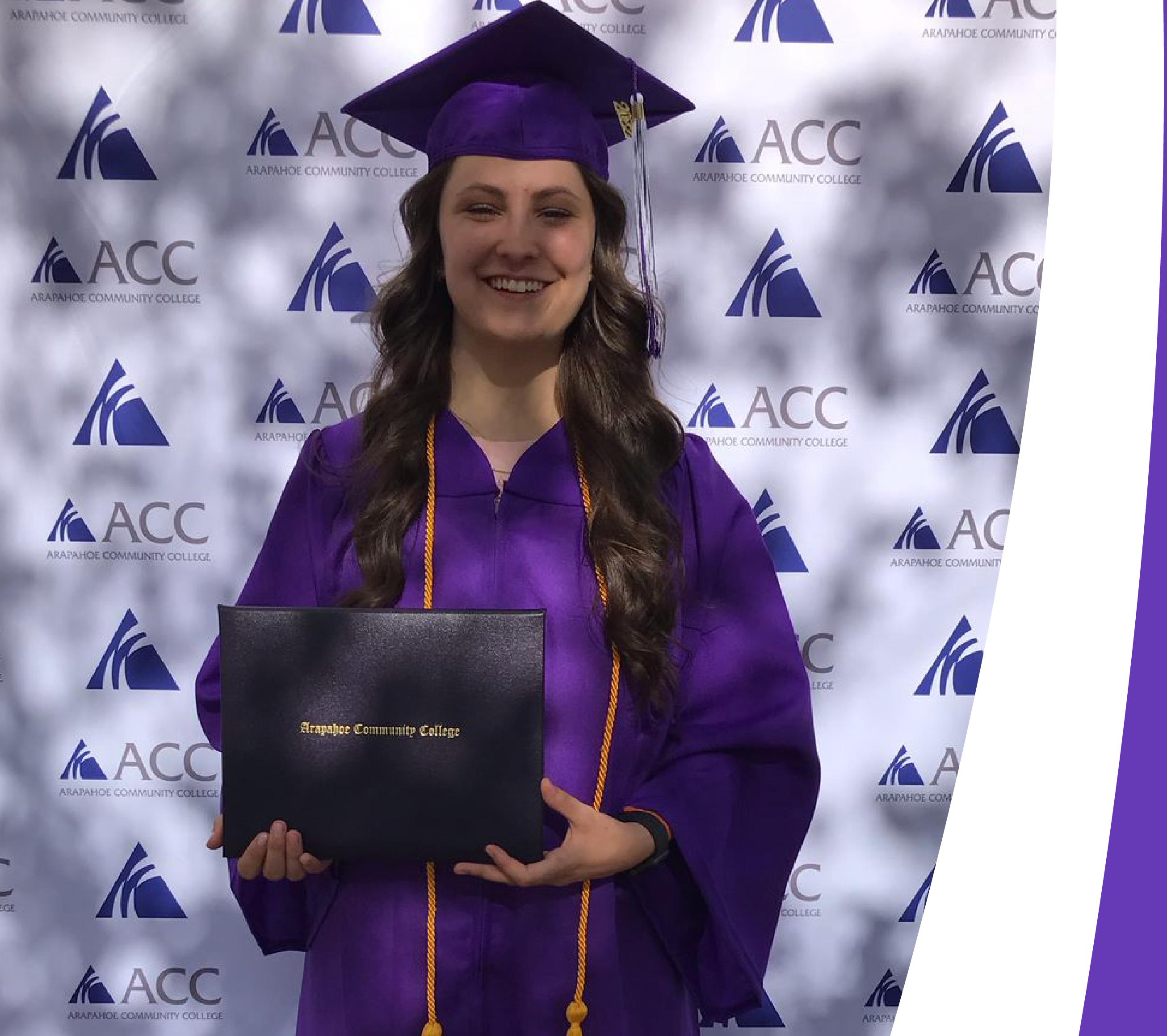
Students who want to pursue a master's degree in construction management should be proficient in precalculus math. The program requires students to understand construction mechanics and the properties. It is important that students have an understanding of contracts and how to estimate. A basic knowledge of construction computer software is necessary. This will help students prepare for the various positions in the industry. These courses should be completed by students interested in the field.
Construction management degrees require math and physics skills
A construction management degree is a combination of math and physics. It teaches students the technical skills needed for managing large-scale construction projects. Learn about building layout and basic structural analysis. Additionally, you'll learn how construction drawings are read. Computers play an important role in all technical courses, and you'll learn about building information modeling and computer-aided drawing. This education can help make you a successful contractor manager by combining solid knowledge about construction principles and industry standards.
Horizontal measurements, differential leveling and transverse loop calculations are all part of surveying operations. Students learn how construction plans are interpreted and created. Students also learn how to use software to calculate costs and prepare takeoffs. They will also study cost estimation, quality standards, sustainable building practices, and the importance of quality assurance. The students will also learn about mechanical and electrical systems. They will also gain real-world experience as a manager of a construction site.
English and foreign languages are required for the construction management degree
For a construction management degree, there are several requirements. These courses are typically completed in the first two years of the program. These courses should be completed by students with a minimum grade of C. Course content is varied, with an emphasis on the fundamental principles of engineering and construction management. The course content requires students to have an understanding of business, law and economics. Students need to be familiar with basic principles and techniques of equipment and structural design. Students must be knowledgeable about safety, health, environmental principles and other aspects of the profession.
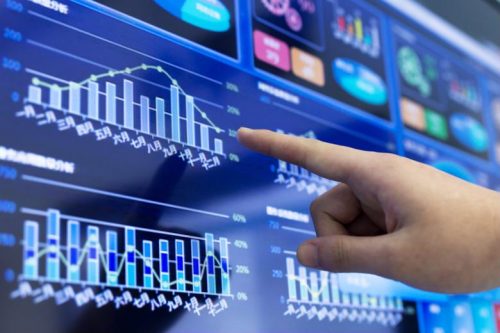
Applicants for the Master of Science in Construction Management degree program must have a bachelor's degree or its equivalent. They should also have some experience in construction that is acceptable to their department. Non-engineering candidates should be prepared to enroll in leveling courses which are not part the program plan. TOEFL scores are required for students who study at non-English-medium Universities. To be accepted to the program, a TOEFL score below 550 is required.
FAQ
What is TQM, exactly?
The industrial revolution led to the birth and growth of the quality movement. Manufacturing companies realized they couldn't compete solely on price. They needed to improve the quality and efficiency of their products if they were to be competitive.
Management responded to the need to improve, and developed Total Quality Management (TQM). This focused on improving every aspect of an organization’s performance. It included continual improvement processes, employee involvement, customer satisfaction, and customer satisfaction.
What's the difference between a program and a project?
A program is permanent, whereas a project is temporary.
A project typically has a defined goal and deadline.
It is often done in a team that reports to another.
A program typically has a set goal and objective.
It is usually implemented by a single person.
What are the four main functions of management?
Management is responsible to plan, organize, direct, and control people and resources. It also includes developing policies and procedures and setting goals.
Management aids an organization in reaching its goals by providing direction and coordination, control, leadership motivation, supervision, training, evaluation, and leadership.
The four main functions of management are:
Planning - This is the process of deciding what should be done.
Organizing: Organizing refers to deciding how things should work.
Directing - This refers to getting people follow instructions.
Controlling: Controlling refers to making sure that people do what they are supposed to.
What are the 3 basic management styles?
The three major management styles are authoritarian (left-faire), participative and laissez -faire. Each style is unique and has its strengths as well as weaknesses. Which style do yo prefer? Why?
Autoritarian - The leader sets direction and expects everyone else to follow it. This style is most effective when an organization is large, stable, and well-run.
Laissez-faire is a leader who allows everyone to make their own decisions. This style is best when the organization has a small but dynamic group.
Participative - Leaders listen to all ideas and suggestions. This style is most effective in smaller organizations, where everyone feels valued.
Statistics
- UpCounsel accepts only the top 5 percent of lawyers on its site. (upcounsel.com)
- 100% of the courses are offered online, and no campus visits are required — a big time-saver for you. (online.uc.edu)
- The profession is expected to grow 7% by 2028, a bit faster than the national average. (wgu.edu)
- Hire the top business lawyers and save up to 60% on legal fees (upcounsel.com)
- As of 2020, personal bankers or tellers make an average of $32,620 per year, according to the BLS. (wgu.edu)
External Links
How To
How can you implement the Kaizen technique?
Kaizen means continuous improvement. Kaizen is a Japanese concept that encourages constant improvement by small incremental changes. It's a process where people work together to improve their processes continuously.
Kaizen is one method that Lean Manufacturing uses to its greatest advantage. Employees responsible for the production line should identify potential problems in the manufacturing process and work together to resolve them. This way, the quality of products increases, and the cost decreases.
The main idea behind kaizen is to make every worker aware of what happens around him/her. It is important to correct any problems immediately if they are discovered. If someone is aware of a problem at work, he/she should inform his/her manager immediately.
Kaizen is based on a few principles. Always start with the end product in mind and work our way back to the beginning. In order to improve our factory's production, we must first fix the machines producing the final product. Next, we repair the machines that make components. Then, the machines that make raw materials. And finally, we fix the workers who work directly with those machines.
This method, called 'kaizen', focuses on improving each and every step of the process. Once we have finished fixing the factory, we return to the beginning and work until perfection.
How to measure kaizen's effectiveness in your business is essential to implement it. There are many ways to tell if kaizen is effective. Another way to determine if kaizen is working well is to look at the quality of the products. Another way is determining how much productivity increased after implementing kaizen.
Another way to know whether kaizen is working is to ask yourself why did you decide to implement kaizen. Did you do it because it was legal or to save money? Did you really think that it would help you achieve success?
Congratulations if you answered "yes" to any of the questions. You are ready to start kaizen.