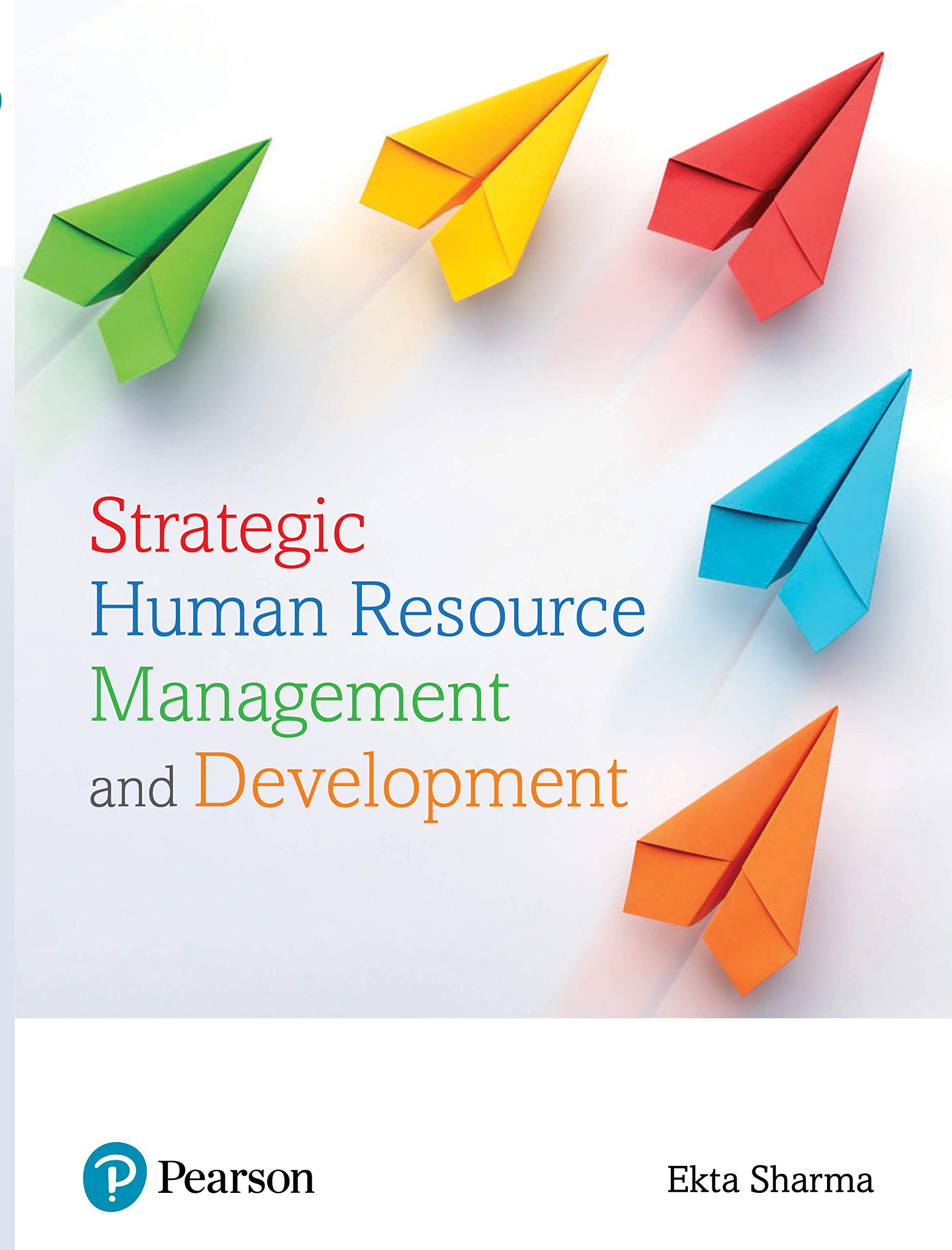
A team manager is responsible for managing a group of people. They manage their workloads and ensure that tasks are completed on time. They are able to resolve conflicts between colleagues and offer constructive feedback. The most successful managers know how to balance their work with their team members' needs. These attributes make team managers effective. These qualities can inspire team members, and boost morale.
Leadership skills
To be a great team manager, leadership skills are essential. It is crucial that team leaders have the ability to think strategically, and translate organizational goals into tangible results. Leaders who lack this skill will cause problems for the organization. They will lose sight on the importance of their team and their role in the organization. Developing strategic thinking requires a leader to step back from current issues and understand the organization's goals and the complexities of internal and external factors.
A team leader must be approachable to others and willing to share their opinions with them. Being able to openly listen is an important skill in leadership. This shows that you have a good understanding of other people's views and can listen to them before you decide how you will deal with them. This skill allows your team to be motivated and recognize their input.
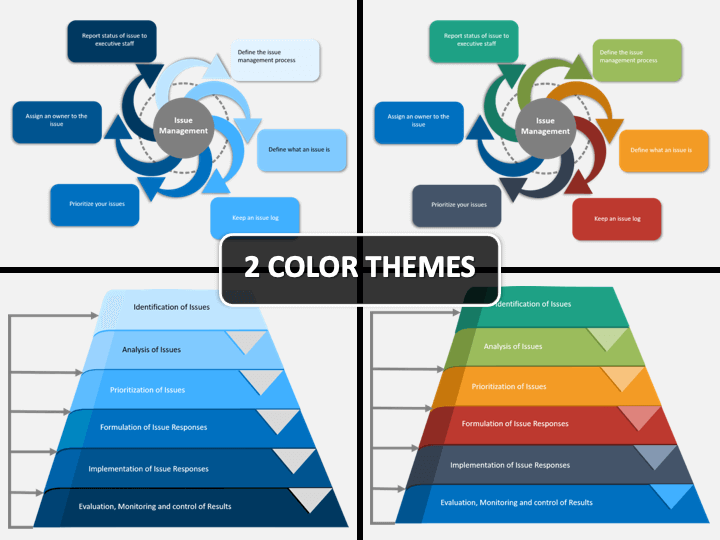
Communication skills
Communication skills are essential in the work environment and in leading a team. A lack of communication skills can be a significant barrier to an organization's success. According to a Gatehouse report, poor communication among managers was the top three cause of ineffective internal communication. Also, only 14% of employees stated that their performance reviews inspired them. Managers must be able to communicate with their team and build relationships. This can be achieved through effective listening and clarifying of their team members' views and ideas.
It is best to be honest and direct when communicating with people. Some employees prefer detail while others prefer generalization. If you know which type your team members prefer, you can adjust your communication style accordingly. The more attention you pay to your team's communication preferences, the more likely they will feel that they are heard and understood.
Skills in organization
Organization skills are crucial if you want to manage a team. These skills help you to manage time, people, and conflict. Being able to prioritize tasks and organize will help you appear more trustworthy and increase your credibility. The ability to think through complex issues and create solutions is a sign of organizational competence. You can also stay calm when under pressure by being organized.
You will communicate better with your colleagues if you have better organization skills. Being organized will help you save time and focus on the most important tasks. Your workspace will make you less productive and could cause stress. Rewriting your to-do lists is a great way to organize your workspace.
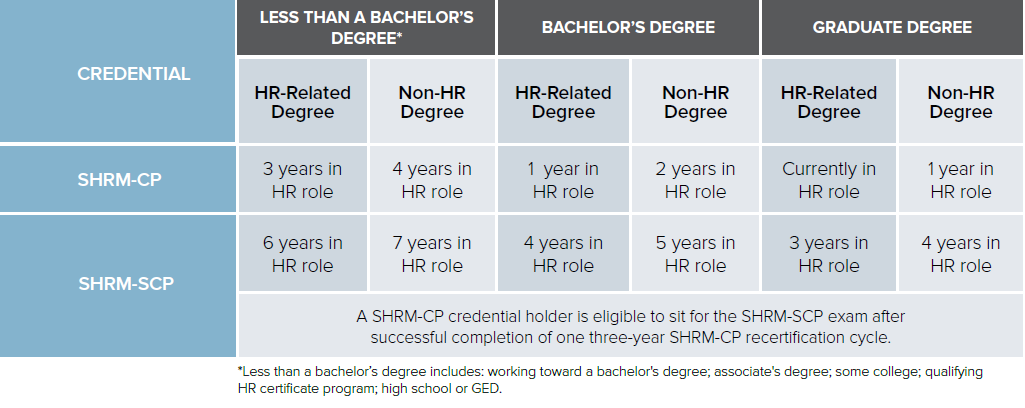
Time management
Time management is a key part of team management. This includes regular check-ins and the use of tools to track the status of each project. Encourage team members to be productive, and celebrate their achievements. Good time management is key to maximizing productivity and preventing overload.
Regardless of the size and structure of your team, time management is critical to the success of your company. A time management strategy that works requires flexibility and adaptability to change. A team alignment is one way to do this. Studies have shown that teams spend two-thirds of their time communicating, connecting, and collaborating. Inefficient communication also accounts for 15% of employees' lost work time.
FAQ
What is the difference between leadership and management?
Leadership is all about influencing others. Management is about controlling others.
A leader inspires his followers while a manager directs the workers.
A leader motivates people to achieve success; a manager keeps workers on task.
A leader develops people; a manager manages people.
What are the top management skills?
Any business owner needs to be able to manage people, finances, resources and time. They are the ability to manage people and finances, space, money, and other factors.
These skills are necessary for setting goals and objectives as well as planning strategies, leading groups, motivating employees and solving problems.
As you can see there is no end to the number of managerial tasks.
What kind of people use Six Sigma?
Six Sigma will most likely be familiar to people who have worked in statistics and operations research. It can be used by anyone in any business aspect.
It is a commitment-intensive task that requires strong leadership skills.
Why is project management important for companies?
Project management techniques are used to ensure that projects run smoothly and meet deadlines.
This is because most businesses rely heavily on project work to produce goods and services.
These projects must be managed efficiently and effectively by companies.
Companies that do not manage their projects effectively risk losing time, money, or reputation.
What role does a manager have in a company's success?
Different industries have different roles for managers.
The manager oversees the day-to-day activities of a company.
He/she is responsible for ensuring that the company meets all its financial obligations and produces the goods or services customers want.
He/she makes sure that employees adhere to the rules and regulations as well as quality standards.
He/she is responsible for the development of new products and services, as well as overseeing marketing campaigns.
How can a manager motivate his/her staff?
Motivation is the desire for success.
Enjoyable activities can motivate you.
Or you can get motivated by seeing yourself making a contribution to the success of the organization.
For example: If you want to be a doctor, you might find it more motivating seeing patients than reading medical books all day.
Motivation comes from within.
Perhaps you have a strong sense to give back, for example.
You may even find it enjoyable to work hard.
If you feel unmotivated, ask yourself why.
Then try to think about ways to change your situation to be more motivated.
What is TQM, exactly?
When manufacturing companies realized that price was not enough to compete, the industrial revolution brought about the quality movement. If they wanted to stay competitive, they needed to improve their quality and efficiency.
Management developed Total Quality Management to address the need for improvement. It focused on all aspects of an organisation's performance. It involved continuous improvement, employee participation, and customer satisfaction.
Statistics
- The BLS says that financial services jobs like banking are expected to grow 4% by 2030, about as fast as the national average. (wgu.edu)
- Our program is 100% engineered for your success. (online.uc.edu)
- As of 2020, personal bankers or tellers make an average of $32,620 per year, according to the BLS. (wgu.edu)
- Your choice in Step 5 may very likely be the same or similar to the alternative you placed at the top of your list at the end of Step 4. (umassd.edu)
- 100% of the courses are offered online, and no campus visits are required — a big time-saver for you. (online.uc.edu)
External Links
How To
How does Lean Manufacturing work?
Lean Manufacturing processes are used to reduce waste and improve efficiency through structured methods. They were developed by Toyota Motor Corporation in Japan during the 1980s. It was designed to produce high-quality products at lower prices while maintaining their quality. Lean manufacturing focuses on eliminating unnecessary steps and activities from the production process. It includes five main elements: pull systems (continuous improvement), continuous improvement (just-in-time), kaizen (5S), and continuous change (continuous changes). The production of only what the customer needs without extra work is called pull systems. Continuous improvement is constantly improving upon existing processes. Just-in-time is when components and other materials are delivered at their destination in a timely manner. Kaizen refers to continuous improvement. It is achieved through small changes that are made continuously. Last but not least, 5S is for sort. To achieve the best results, these five elements must be used together.
Lean Production System
Six key concepts make up the lean manufacturing system.
-
Flow - The focus is on moving information and material as close as possible to customers.
-
Value stream mapping: This is a way to break down each stage into separate tasks and create a flowchart for the entire process.
-
Five S’s - Sorted, In Order. Shine. Standardize. And Sustain.
-
Kanban is a visual system that uses visual cues like stickers, colored tape or stickers to keep track and monitor inventory.
-
Theory of constraints - identify bottlenecks during the process and eliminate them with lean tools like Kanban boards.
-
Just-intime - Order components and materials at your location right on the spot.
-
Continuous improvement - incremental improvements are made to the process, not a complete overhaul.