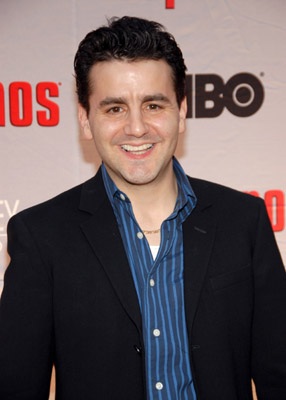
It is necessary to possess the skills and qualifications needed to work as a construction worker. There are many occupations within the construction industry. These classes will enable you to understand the many trades available in the construction industry. They will also show you how to use blueprints, specifications, and plans. You will also get to practice the use of power tools and measuring equipment.
Overview of construction industry
There are many types of work in the construction industry. Some projects are small while others require extensive expertise. You can also find specialized companies that specialize in one type of work. We will be looking at the role of different types and how they differ from other sectors in the construction industry.
Although the overall growth rate of the construction industry has been slow, it still faces many challenges. An increasing population puts more pressure on infrastructure and housing.
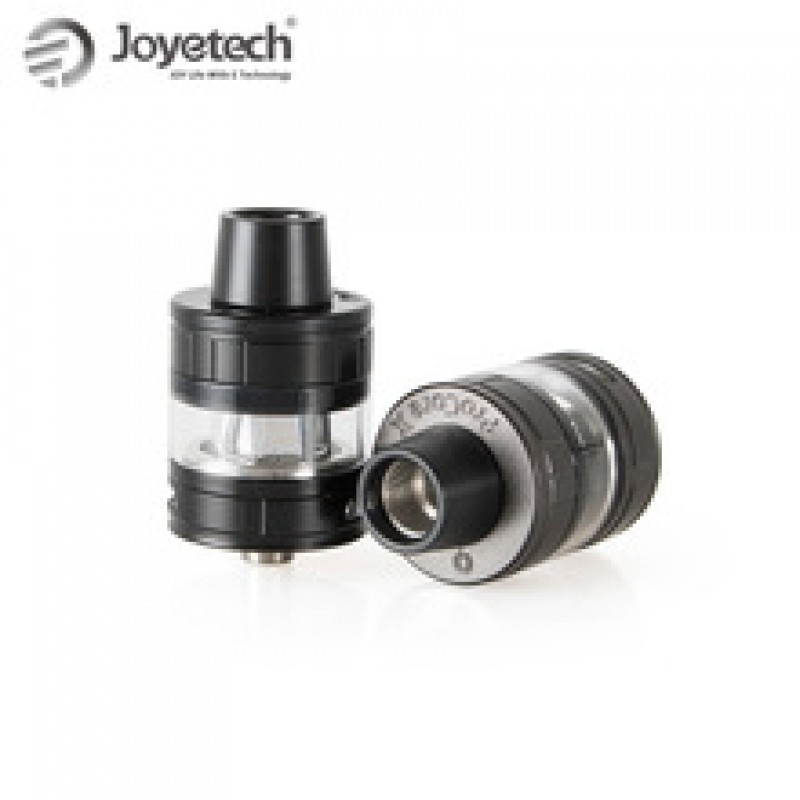
Career opportunities in the industry
There are many career options for those who are interested in the construction sector. It doesn't matter if you're an expert or just looking to learn more about the field. There are many avenues that can help you get in the door. The Bureau of Labor Statistics expects that the construction industry will expand by nearly 10% over the next decade. It is a promising career choice. It is also a highly diverse industry with more women and minorities working in it.
For those who have an engineering or construction degree, the construction industry has many career options. A project manager is a job that requires problem solving skills. They oversee all aspects of a project including budgeting, coordination, planning, and budgeting. They need to be strong leaders and have great problem-solving skills. Additionally, they must have a degree or certificate in construction management, surveying, or civil engineering. Many project managers are trained as construction engineers before moving into management.
You need to have the right skills to work in this industry
It takes a broad range of skills to work in the construction industry. You will need to be capable of reading construction documents and accurately calculating measurements. You will also need to have basic math and English language skills. Effective communication is essential when working in a construction environment.
You will need to have skills such as bricklaying, carpentry, and cement pouring. Other skills can include putting up drywall and using specific types of equipment. For any position in construction, you must be able to think critically and work within tight deadlines. Moreover, there are a variety of soft skills that you will need to succeed in the construction industry, including conflict management, communication skills, and collaboration.
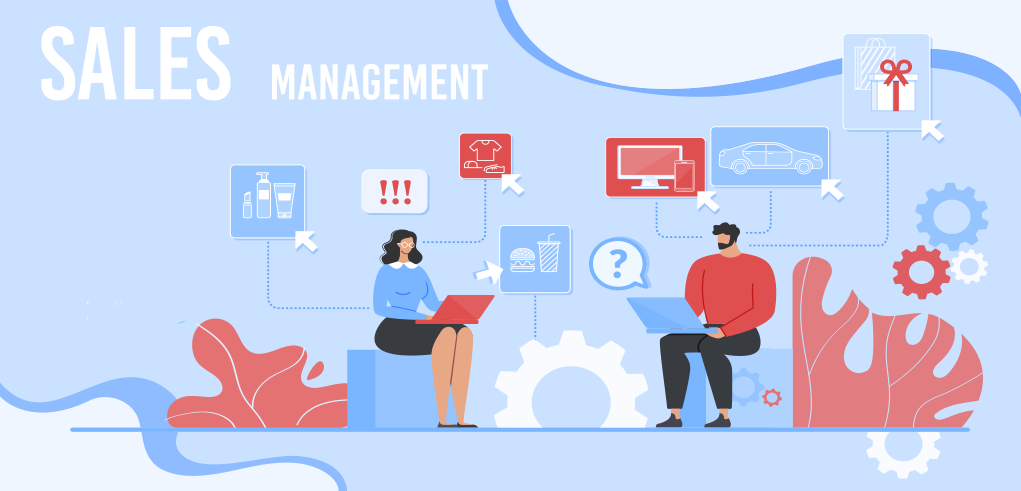
The industry requires that you have the right educational qualifications
Educational requirements for entry into the construction industry vary depending on the specific type of occupation you'd like to pursue. You can gain the skills you need to succeed in this trade through apprenticeship programs or college courses. You can also take an OSHA certification course to get a better understanding of safety regulations. There are also specialty certifications available, which train you for certain types of work sites. These courses are available online, or can be done in person.
A certificate in construction can be obtained or an associate's in construction management. Most construction management programs take approximately two years to complete. They will teach you the practical skills that are necessary to succeed in the sector. There are also programs that teach you business aspects of the industry.
FAQ
What is the difference in Six Sigma and TQM?
The main difference in these two quality management tools lies in the fact that six sigma is focused on eliminating defects and total quality management (TQM), emphasizes improving processes and reducing costs.
Six Sigma is a method for continuous improvement. It emphasizes the elimination or minimization of defects through statistical methods such control charts and p charts.
The goal of this method is to reduce variation in product output. This is done by identifying root causes and rectifying them.
Total quality management includes monitoring and measuring all aspects of an organization's performance. It also includes training employees to improve performance.
It is often used to increase productivity.
What is the best way to motivate your employees as a manager?
Motivation refers to the desire or need to succeed.
Engaging in something fun can be a great way to get motivated.
You can also be motivated by the idea of making a difference to the success and growth of your organization.
If you are a doctor and want to be one, it will likely be more rewarding to see patients than to read medical books every day.
Another type of motivation comes from within.
Perhaps you have a strong sense to give back, for example.
You may even find it enjoyable to work hard.
If you feel unmotivated, ask yourself why.
Then, consider ways you could improve your motivation.
What is Kaizen?
Kaizen, a Japanese term that means "continuous improvement," is a philosophy that encourages employees and other workers to continuously improve their work environment.
Kaizen is founded on the belief of everyone being able to do their job well.
What are the main styles of management?
The three basic management styles are: authoritarian, laissez-faire, and participative. Each style has its advantages and disadvantages. Which style do YOU prefer? Why?
Autoritarian - The leader sets direction and expects everyone else to follow it. This style is most effective when an organization is large, stable, and well-run.
Laissez-faire – The leader gives each individual the freedom to make decisions for themselves. This style is best when the organization has a small but dynamic group.
Participative – The leader listens and takes in ideas from all. This style is best for small organizations where everyone feels valued.
Statistics
- As of 2020, personal bankers or tellers make an average of $32,620 per year, according to the BLS. (wgu.edu)
- 100% of the courses are offered online, and no campus visits are required — a big time-saver for you. (online.uc.edu)
- This field is expected to grow about 7% by 2028, a bit faster than the national average for job growth. (wgu.edu)
- Our program is 100% engineered for your success. (online.uc.edu)
- Your choice in Step 5 may very likely be the same or similar to the alternative you placed at the top of your list at the end of Step 4. (umassd.edu)
External Links
How To
How do you apply the Kaizen method to your life?
Kaizen means continuous improvement. This term was first used by Toyota Motor Corporation in the 1950s. It refers to the Japanese philosophy that emphasizes continuous improvement through small incremental changes. It's a team effort to continuously improve processes.
Kaizen is one method that Lean Manufacturing uses to its greatest advantage. Kaizen is a concept where employees in charge of the production line are required to spot problems during the manufacturing process before they become major issues. This will increase the quality and decrease the cost of the products.
Kaizen is the idea that every worker should be aware of what is going on around them. It is important to correct any problems immediately if they are discovered. If someone spots a problem while at work, they should immediately report it to their manager.
When doing kaizen, there are some principles we must follow. Start with the end product, and then move to the beginning. To improve our factory, for example, we need to fix the machines that produce the final product. Next, we repair the machines that make components. Then, the machines that make raw materials. Then, we fix those who work directly with the machines.
This method, called 'kaizen', focuses on improving each and every step of the process. When we are done fixing the whole factory, we go back to the beginning and continue until we reach perfection.
You need to know how to measure the effectiveness of kaizen within your business. There are several ways that you can tell if your kaizen system is working. One of these ways is to check the number of defects found on the finished products. Another method is to determine how much productivity has improved since the implementation of kaizen.
If you want to find out if your kaizen is actually working, ask yourself why. Did you do it because it was legal or to save money? Did you really believe it would lead to success?
Suppose you answered yes to any of these questions, congratulations! Now you're ready for kaizen.