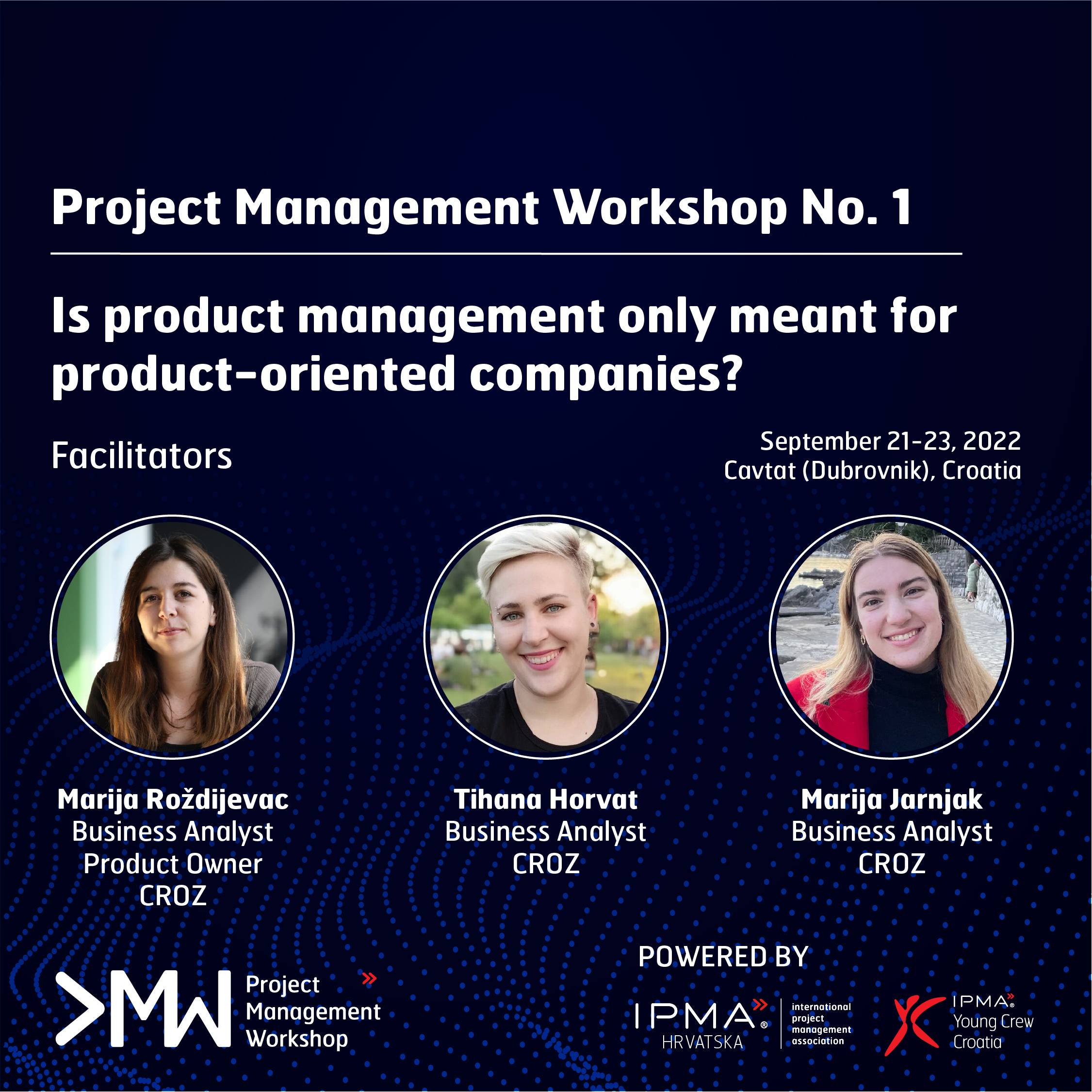
The creation of risk management plans is an important part of any project, from small to large. A risk management plan can help you reduce the risks associated a project. Here are some guidelines for creating a project risk management plan. Before you begin to write, make sure you have assessed all potential risks. This will help you identify risks that are most likely to have the greatest impact on your business and develop a plan to reduce them. You should ensure that your plan is current and complete so you can implement it quickly.
A risk management plan should be created
A risk management plan can be a valuable tool for managing risks and increasing the likelihood of your project's success. It will help reduce or completely eliminate potential risks and make it easier for you to prepare your team. Your project's success is guaranteed by a well-defined risk management program. It can also cause problems if not done correctly. A risk management plan should be simple, concise, and easily understood.
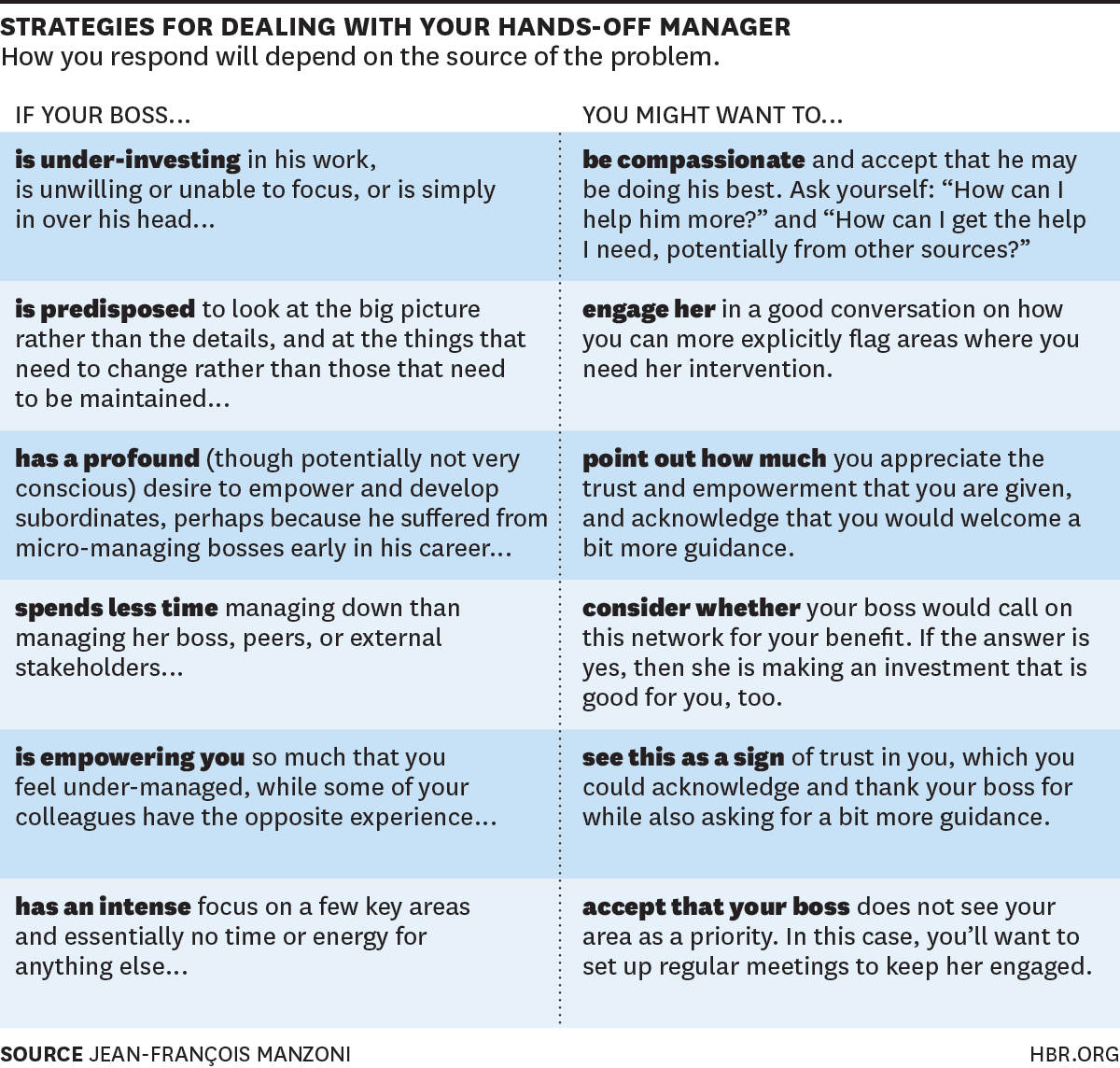
Steps for creating a plan
First, identify the risks and potential solutions. This step should be done collaboratively and includes the input of team members and subject matter experts. The next step is to identify risks and determine the resources necessary to mitigate or prevent them. As this will keep the team on task and focused, the risk management plan should include communication plans. The plan should also contain a list containing all possible solutions and mitigation measures.
Analyze project risks
A project's risk management plan is an integral part of its overall plan. A risk analysis helps to identify the most at-risk aspects of a project. Once potential risks are identified, project managers can decide what steps to take to mitigate them. A sound risk management plan will include steps that can be taken to minimize risks and minimize the impact. In this article we will talk about the different steps involved and how to analyze project risks.
Create a plan to minimize them
It is vital to have a strategy for managing risk. This plan will identify and prioritize risks for your business and help you minimize the negative impact of these risks. You cannot delegate this responsibility to one person. It is essential to inform employees about risks and train them in mitigation strategies. Your risk mitigation strategy will only be as effective as your people and the resources you have available. By using a risk management system, you can keep your business running smoothly.
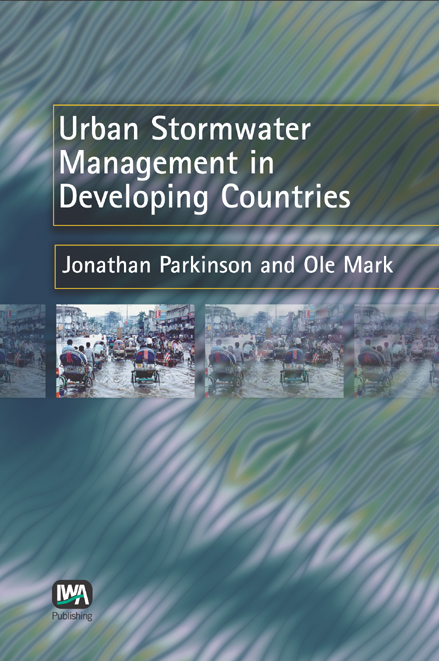
Archive your plan
Archiving your risk management plans is required in some organizations. But not all risk management programs will work for every project. An archived risk management program from a previous project may be able to provide a solid foundation for future projects. Archiving your risk management plan may be optional, but it is always a good idea to do it. These are some suggestions for how to archive your plan. We hope you find these tips useful!
FAQ
What is a basic management tool used in decision-making?
A decision matrix can be a simple, but effective tool to assist managers in making decisions. It allows them to think through all possible options.
A decision matrix is a way of representing alternatives as rows and columns. This allows one to see how each alternative impacts other options.
In this example, there are four possible options represented by boxes on the left-hand side of the matrix. Each box represents an alternative. The top row depicts the current status quo, while the bottom row represents what would happen if no action was taken.
The effect of selecting Option 1 is shown in the middle column. In this case, it would mean increasing sales from $2 million to $3 million.
The next two columns show the effects of choosing Options 2 and 3. These are both positive changes that increase sales by $1million and $500,000. These changes can also have negative effects. Option 2 can increase costs by $100 million, while Option 3 can reduce profits by $200,000.
The final column shows the results for Option 4. This will result in sales falling by $1,000,000
The best thing about using a decision matrix is that you don't need to remember which numbers go where. It's easy to see the cells and instantly know if any one of them is better than another.
This is because your matrix has already done the hard work. It's as easy as comparing numbers in the appropriate cells.
Here's a sample of how you might use decision matrixes in your business.
It is up to you to decide whether to spend more money on advertising. This will allow you to increase your revenue by $5000 per month. You will still have to pay $10000 per month in additional expenses.
By looking at the cell just below "Advertising", the net result can be calculated as $15 thousand. Advertising is worth more than its cost.
How does Six Sigma work
Six Sigma uses statistics to measure problems, find root causes, fix them, and learn from past mistakes.
The first step in solving a problem is to identify it.
The data is then analyzed and collected to identify trends.
The problem is then rectified.
The data are then reanalyzed to see if the problem is solved.
This continues until the problem has been solved.
How can a manager motivate employees?
Motivation refers to the desire or need to succeed.
Enjoyable activities can motivate you.
Another way to get motivated is to see yourself as a contributor to the success of the company.
For example: If you want to be a doctor, you might find it more motivating seeing patients than reading medical books all day.
A different type of motivation comes directly from the inside.
For example, you might have a strong sense of responsibility to help others.
Perhaps you enjoy working hard.
If you feel unmotivated, ask yourself why.
Then, consider ways you could improve your motivation.
What is Kaizen and how can it help you?
Kaizen refers to a Japanese term that stands for "continuous improvements." It is a philosophy which encourages employees in continuously improving their work environment.
Kaizen is a belief that everyone should have the ability to do their job well.
What are the top management skills?
Managerial skills are crucial for every business owner, regardless of whether they run a small store in their locality or a large corporation. These skills include the ability manage people, finances and resources as well as other factors.
Managerial skills are required when setting goals and objectives and planning strategies, leading employees, motivating them, solving problems, creating policies, procedures, or managing change.
As you can see, there's no end to the list of managerial duties!
What does it mean to say "project management"
This refers to managing all activities that are involved in a project's execution.
We include defining the scope of the project, identifying the requirements, preparing the budget, organizing the project team, scheduling the work, monitoring progress, evaluating results, and closing down the project.
Statistics
- The profession is expected to grow 7% by 2028, a bit faster than the national average. (wgu.edu)
- The average salary for financial advisors in 2021 is around $60,000 per year, with the top 10% of the profession making more than $111,000 per year. (wgu.edu)
- The BLS says that financial services jobs like banking are expected to grow 4% by 2030, about as fast as the national average. (wgu.edu)
- UpCounsel accepts only the top 5 percent of lawyers on its site. (upcounsel.com)
- This field is expected to grow about 7% by 2028, a bit faster than the national average for job growth. (wgu.edu)
External Links
How To
How is Lean Manufacturing done?
Lean Manufacturing uses structured methods to reduce waste, increase efficiency and reduce waste. They were developed in Japan by Toyota Motor Corporation (in the 1980s). It was designed to produce high-quality products at lower prices while maintaining their quality. Lean manufacturing emphasizes removing unnecessary steps from the production process. It has five components: continuous improvement and pull systems; just-in time; continuous change; and kaizen (continuous innovation). The production of only what the customer needs without extra work is called pull systems. Continuous improvement involves constantly improving upon existing processes. Just-intime refers the time components and materials arrive at the exact place where they are needed. Kaizen means continuous improvement. Kaizen involves making small changes and improving continuously. Finally, 5S stands for sort, set in order, shine, standardize, and sustain. To achieve the best results, these five elements must be used together.
Lean Production System
Six key concepts underlie the lean production system.
-
Flow - The focus is on moving information and material as close as possible to customers.
-
Value stream mapping - break down each stage of a process into discrete tasks and create a flowchart of the entire process;
-
Five S's, Sort, Set in Order, Shine. Standardize. and Sustain.
-
Kanban is a visual system that uses visual cues like stickers, colored tape or stickers to keep track and monitor inventory.
-
Theory of constraints - identify bottlenecks during the process and eliminate them with lean tools like Kanban boards.
-
Just-intime - Order components and materials at your location right on the spot.
-
Continuous improvement is making incremental improvements to your process, rather than trying to overhaul it all at once.