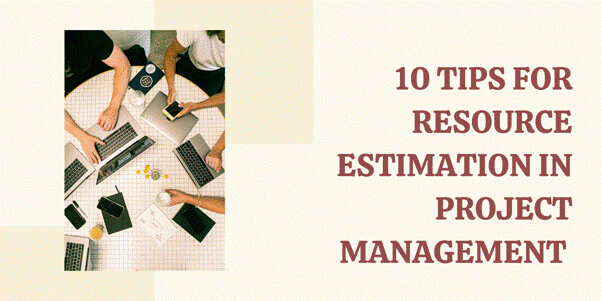
It is crucial to create a positive environment at work in order to ensure the well-being of your employees. This promotes higher productivity, lowers burnout, decreases complaints, and helps to reduce stress. Several studies have shown that employees who are happy and motivated work more effectively. There are several things to keep in mind when creating a positive workplace environment.
Positive work environments are conducive to productivity
Positive working environments create a calm environment that encourages employees to be more productive and stay focused. This environment promotes cognitive and physical well-being, and it is often marked by clear communication between employees as well as management. This type of environment is conducive to employee growth and development by giving them the opportunity to ask questions and give constructive feedback.
Moreover, a positive work environment encourages employees to give 200% of their best efforts. They take full responsibility for their actions and do not seek revenge when receiving negative feedback. It encourages cooperation and camaraderie as well as healthy competition. It also encourages employees who work hard to take breaks and have fun.
Employees feel happier
A positive working environment is a great way to make your employees happy. Employees who are happy at work are more likely to be productive, and they are more likely to share their ideas with their colleagues. They also feel less stressed and more satisfied, and are less likely to take sick days.
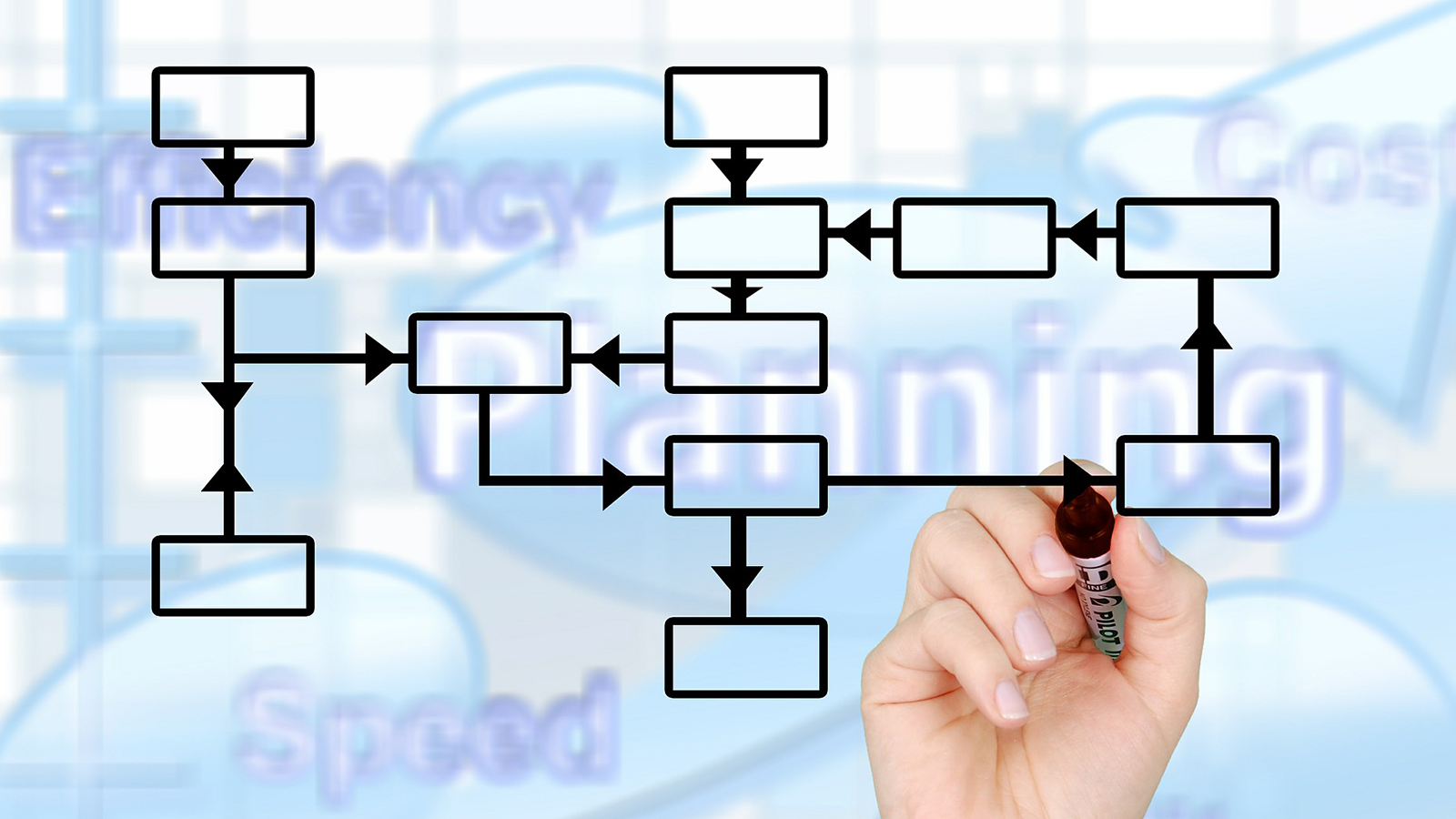
University of Birmingham research showed that employees feel happier when there is a positive workplace. Happy employees perform better and make more sales calls per hour. They also adhere to their work schedule.
Reduced burnout
Effective prevention strategies are vital to ensure that your organization is not at risk of losing its productivity and health. Burnout can affect working relationships and is a psychosocial condition. It's characterized by lack of empathy and emotional detachedness from patients or colleagues. Research has shown that there are proactive ways to avoid this condition, including creating a positive environment at work.
Positive work environments can reduce stress and increase individual and collective efficacy. Empowerment helps increase individual efficacy. It also buffers the effects of exhaustion from cynicism. The quality of communication among staff increases team efficacy, which is related to personal efficacy.
It decreases complaints
Positive working environments make employees feel happy about their jobs. Employees in such an environment are more likely to remain focused on their tasks and complete them in a timely manner. They are more productive and enjoy higher employee status. Positive working environments promote collaboration. Employees have the opportunity to voice their opinions and get feedback in order for them to improve.
Positive working conditions for employees can reduce the amount of complaints made by employees. The first step in creating a positive working environment is to eliminate harassment, bullying and discrimination. Workplaces that are free of harassment and discrimination are a great place for employees to work. Positive workplaces increase employee morale and reduce complaints.
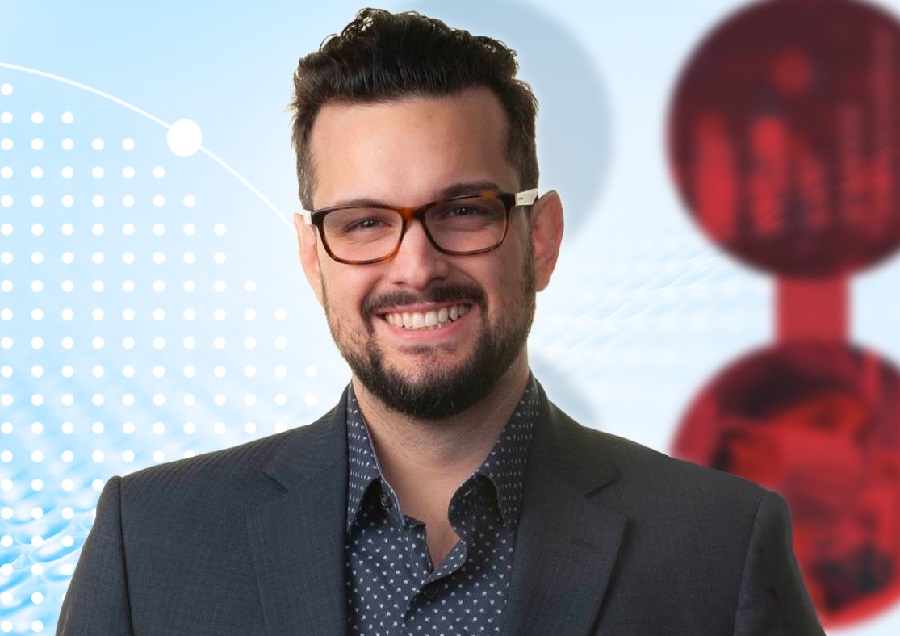
It helps teachers feel better
The quality of a teacher's working environment can impact his or her wellbeing. There are many ways to improve teacher wellness, including providing a supportive environment for staff and hosting regular meetings. An audit can be done to assess the health of teachers and give them a starting point for improvement.
Teachers interact with thousands of people every day. Their well-being is dependent on the quality of those interactions. Studies have shown that a toxic culture can lead to poor teacher wellbeing. Supportive environments will encourage healthy behaviors and allow teachers to be more focused on their students. Regular professional development is also important for educators. Teachers want PD to improve teacher wellbeing. This is according to a survey.
FAQ
What are some common mistakes managers make?
Sometimes, managers make their job more difficult than it is.
They may not be able to delegate enough responsibility to staff or provide adequate support.
A majority of managers lack the communication skills needed to motivate their team and lead them.
Some managers set unrealistic expectations for their staff.
Some managers may try to solve every problem themselves instead of delegating responsibility to others.
What is the main difference between Six Sigma Six Sigma TQM and Six Sigma Six Sigma?
The main difference between these two quality management tools is that six sigma focuses on eliminating defects while total quality management (TQM) focuses on improving processes and reducing costs.
Six Sigma is a methodology for continuous improvement. It emphasizes the elimination and improvement of defects using statistical methods, such as control charts, P-charts and Pareto analysis.
This method has the goal to reduce variation of product output. This is done by identifying and correcting the root causes of problems.
Total Quality Management involves monitoring and measuring every aspect of the organization. It also includes the training of employees to improve performance.
It is often used to increase productivity.
What is Six Sigma?
It's an approach to quality improvement that emphasizes customer service and continuous learning. This is an approach to quality improvement that uses statistical techniques to eliminate defects.
Motorola invented Six Sigma in 1986 as part its efforts to improve manufacturing.
The idea quickly spread in the industry. Many organizations today use six-sigma methods to improve product design and production, delivery and customer service.
What is Kaizen?
Kaizen is a Japanese term which means "continuous improvement." This philosophy encourages employees to continually look for ways to improve the work environment.
Kaizen is founded on the belief of everyone being able to do their job well.
Statistics
- Hire the top business lawyers and save up to 60% on legal fees (upcounsel.com)
- As of 2020, personal bankers or tellers make an average of $32,620 per year, according to the BLS. (wgu.edu)
- The average salary for financial advisors in 2021 is around $60,000 per year, with the top 10% of the profession making more than $111,000 per year. (wgu.edu)
- This field is expected to grow about 7% by 2028, a bit faster than the national average for job growth. (wgu.edu)
- 100% of the courses are offered online, and no campus visits are required — a big time-saver for you. (online.uc.edu)
External Links
How To
How can you use the Kaizen method?
Kaizen means continuous improvement. The Japanese philosophy emphasizes small, incremental improvements to achieve continuous improvement. This term was created by Toyota Motor Corporation in 1950. It's a team effort to continuously improve processes.
Kaizen, a Lean Manufacturing method, is one of its most powerful. In this concept, employees who are responsible for the production line must identify problems that exist during the manufacturing process and try to solve them before they become big issues. This increases the quality of products and reduces the cost.
The main idea behind kaizen is to make every worker aware of what happens around him/her. To prevent problems from happening, any problem should be addressed immediately. If someone spots a problem while at work, they should immediately report it to their manager.
Kaizen follows a set of principles. The end product is always our starting point and we work toward the beginning. To improve our factory, for example, we need to fix the machines that produce the final product. We then fix the machines producing components, and the machines producing raw materials. And finally, we fix the workers who work directly with those machines.
This method, called 'kaizen', focuses on improving each and every step of the process. When we are done fixing the whole factory, we go back to the beginning and continue until we reach perfection.
You need to know how to measure the effectiveness of kaizen within your business. There are several ways that you can tell if your kaizen system is working. Another method is to see how many defects are found on the products. Another method is to determine how much productivity has improved since the implementation of kaizen.
Another way to know whether kaizen is working is to ask yourself why did you decide to implement kaizen. Did you do it because it was legal or to save money? Did you really think that it would help you achieve success?
Congratulations if you answered "yes" to any of the questions. You are ready to start kaizen.