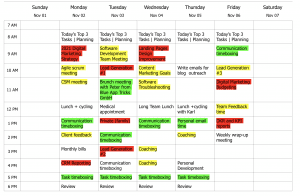
Value at risk (or value at risk) is a calculation which estimates the possibility of investment loss. Normally, this calculation estimates how much an investment can lose in a single day. It can take into consideration other factors such as market volatility. Therefore, this calculation is crucial for anyone investing in stocks and bonds. It will help you choose the right investments for you based upon your risk tolerance and goals. To plan your retirement strategy, you can also use the value at Risk calculation.
Probability of losing certain amounts based on the amount of money that is risked
Probabilities are used when we invest to determine our chances of success. There is a 12% chance we'll lose our $10,000 invested in stocks. In the event of a loss, this is the amount that you have lost. For example, we could lose $5,000 on an investment and suffer $4000 of damage. It is important to understand that probability doesn't guarantee success.
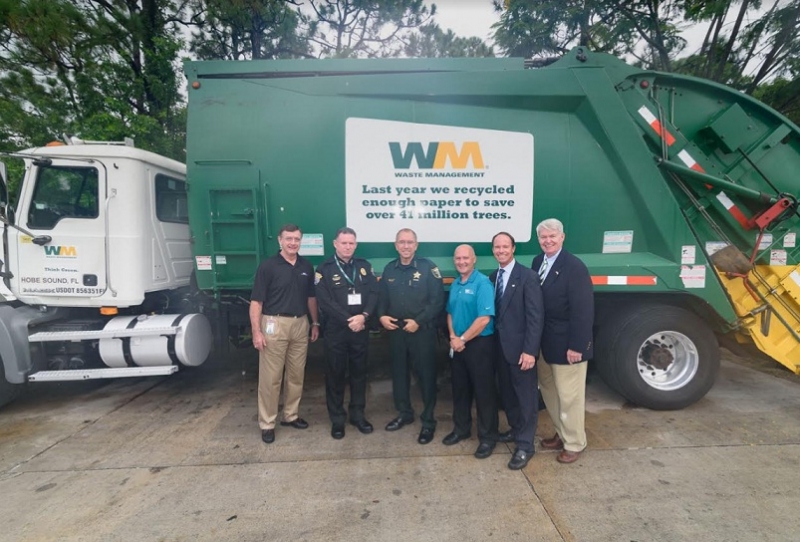
Calculation for VaR
The value at risk tool is important to use when deciding how much risk you want to take on an investment. Based on past performance, value at risk is the probability that you will lose money. It also considers the current market conditions. It can also be used to calculate the average loss for a portfolio. It is easy to calculate value at risk. The portfolio's expected loss in 5% is the percentage value.
Monte Carlo method
The Monte Carlo method is a common tool in financial risk management. It is flexible and can be used in a variety of situations, making it one of the most powerful VAR approaches. It simulates complex pricing patterns and nonlinear risks. This method also allows for longer time horizons, which are necessary for risk measurement and more complex model development. However, there are many limitations to this method.
Historical method
The Historical method to value at risk (VaR), is a popular investment strategy. It uses historical data as a basis for estimating risk factors. This data is then applied to current market values. It's a simple and intuitive way of calculating VaR. This is the maximum loss for a given period. A VaR calculation can only be as accurate as the data points used. To maximize accuracy, it is essential to capture market changes such as major crises.
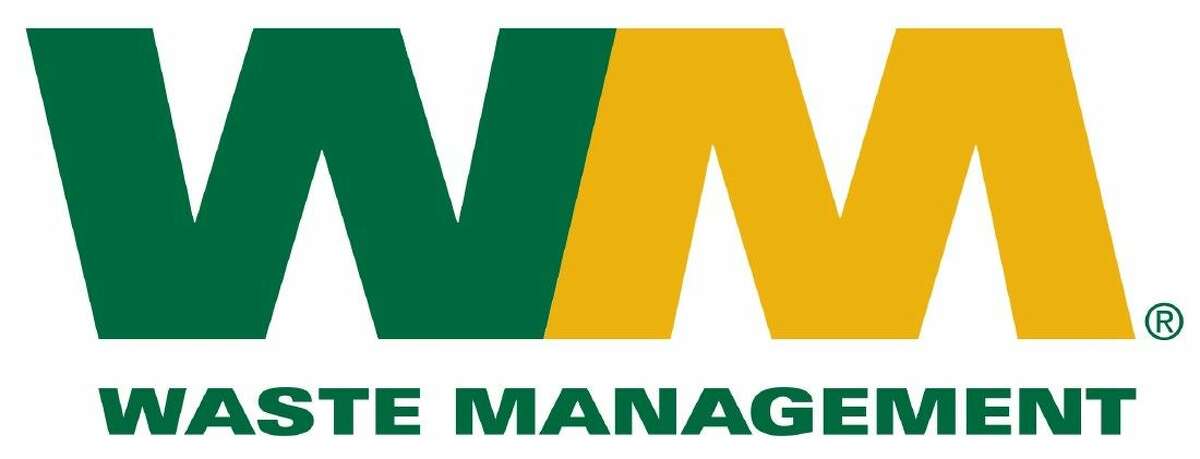
Effects of VaR on liquidity
Value at risk, or VaR, is a measure of the riskiness of an asset. It is calculated as the ratio between the current value of the asset and the expected future value. This measure of risk is most used by financial institutions. The mathematical model used to calculate the concept focuses on rare events. The risk distribution is parametric, with the mass of the distribution at the mean, and the tails at a low level. For example, the FTSE Index has five such days over a 25-year span.
FAQ
What role does a manager play in a company?
Different industries have different roles for managers.
A manager generally manages the day to-day operations in a company.
He/she ensures the company meets its financial commitments and produces goods/services that customers demand.
He/she ensures that employees follow the rules and regulations and adhere to quality standards.
He/she designs new products or services and manages marketing campaigns.
What are the 5 management processes?
Each business has five stages: planning, execution and monitoring.
Planning is about setting goals for your future. Planning involves defining your goals and how to get there.
Execution is the actual execution of the plans. You need to make sure they're followed by everyone involved.
Monitoring is checking on progress towards achieving your objectives. Regular reviews should be done of your performance against targets or budgets.
At the end of every year, reviews take place. They are a chance to see if everything went smoothly during the year. If not, then it may be possible to make adjustments in order to improve performance next time.
After the annual review, evaluation takes place. It helps you identify the successes and failures. It provides feedback about how people perform.
What is TQM exactly?
The industrial revolution was when companies realized that they couldn't compete on price alone. This is what sparked the quality movement. They had to improve efficiency and quality if they were to remain competitive.
Management responded to the need to improve, and developed Total Quality Management (TQM). This focused on improving every aspect of an organization’s performance. It included continuous improvement and employee involvement as well as customer satisfaction.
What are your main management skills
No matter if they are running a local business or an international one, management skills are vital. They are the ability to manage people and finances, space, money, and other factors.
Managerial skills are required when setting goals and objectives and planning strategies, leading employees, motivating them, solving problems, creating policies, procedures, or managing change.
You can see that there are many managerial duties.
How do you effectively manage employees?
Managing employees effectively means ensuring that they are happy and productive.
This includes setting clear expectations for their behavior and tracking their performance.
Managers need clear goals to be able to accomplish this.
They should communicate clearly to staff members. And they need to ensure that they reward good performance and discipline poor performers.
They should also keep records of all activities within their team. These include:
-
What did you accomplish?
-
What was the work involved?
-
Who did it and why?
-
What was the moment it was completed?
-
Why was this done?
This information can be used to monitor performance and evaluate results.
What kind of people use Six Sigma
Six Sigma is well-known to those who have worked in operations research and statistics. It can be used by anyone in any business aspect.
Because it requires a high degree of commitment, only leaders with strong leadership skills can implement it successfully.
Statistics
- As of 2020, personal bankers or tellers make an average of $32,620 per year, according to the BLS. (wgu.edu)
- Your choice in Step 5 may very likely be the same or similar to the alternative you placed at the top of your list at the end of Step 4. (umassd.edu)
- The average salary for financial advisors in 2021 is around $60,000 per year, with the top 10% of the profession making more than $111,000 per year. (wgu.edu)
- The profession is expected to grow 7% by 2028, a bit faster than the national average. (wgu.edu)
- Hire the top business lawyers and save up to 60% on legal fees (upcounsel.com)
External Links
How To
How can Lean Manufacturing be done?
Lean Manufacturing is a method to reduce waste and increase efficiency using structured methods. These processes were created by Toyota Motor Corporation, Japan in the 1980s. The main goal was to produce products at lower costs while maintaining quality. Lean manufacturing focuses on eliminating unnecessary steps and activities from the production process. It includes five main elements: pull systems (continuous improvement), continuous improvement (just-in-time), kaizen (5S), and continuous change (continuous changes). Pull systems allow customers to get exactly what they want without having to do extra work. Continuous improvement involves constantly improving upon existing processes. Just-intime refers the time components and materials arrive at the exact place where they are needed. Kaizen means continuous improvement. Kaizen involves making small changes and improving continuously. Last but not least, 5S is for sort. These five elements can be combined to achieve the best possible results.
Lean Production System
Six key concepts form the foundation of the lean production system:
-
Flow - The focus is on moving information and material as close as possible to customers.
-
Value stream mapping: This is a way to break down each stage into separate tasks and create a flowchart for the entire process.
-
Five S's - Sort, Set In Order, Shine, Standardize, and Sustain;
-
Kanban - visual cues such as stickers or colored tape can be used to track inventory.
-
Theory of constraints: Identify bottlenecks and use lean tools such as kanban boards to eliminate them.
-
Just-in-time - deliver components and materials directly to the point of use;
-
Continuous improvement - make incremental improvements to the process rather than overhauling it all at once.