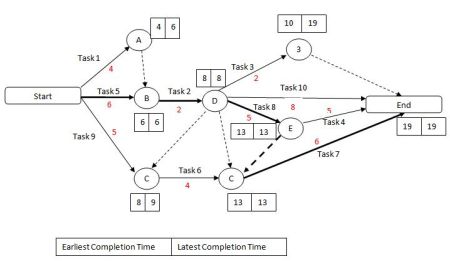
Integrated supply chain management is a holistic approach to managing a business. It is the "cradleto grave" management of businesses. This management approach involves asymmetrical relationships between buyers or sellers. It aims to improve quality and decrease costs. It also involves end-to-end visibility. This is an important aspect of fully integrated supply networks. This approach is not for everyone.
Integrated supply chain management is a "cradle to grave" approach
Integrated supply chain management is an all-encompassing concept that addresses all aspects of the product life cycle, from raw materials to consumer products. It involves forward and reverse logistics, information flows, and cash flows, typically from producers to distributors to retailers. The ultimate goal should be to minimize waste and maximize benefits to the end user. Supply chain managers must be able to recognize and use other resources, as well as recycle materials at the ends of their lives.
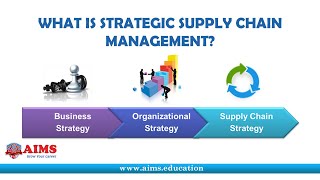
It is marked by adversarial relationships between buyers, sellers, and other participants
The process of integrating supply chain management involves reducing the number of transactions and maximizing the performance of the supply chain. It requires disciplined management skills, technologies and processes. Additionally, it requires a focus on key capabilities. The ultimate goal is higher profitability and reduced risk to all participants. It is difficult to achieve this goal in today's global economic environment. With some common practices and a few key points, it is possible to integrate supply chain management.
It reduces costs
Integrated supply chain management can lower the costs of your business in many ways. First, make sure that your suppliers fulfill your specifications. Second, ensure that they are able to deliver the goods at a fair price. It is important to choose vendors with a solid reputation who can deliver the goods promptly. This is especially important for those who deal with perishable items. Implementing efficient supply chain management techniques can improve the efficiency of your company.
It improves quality
Integrated supply chain management is a single, centralized view that shows all of an organization's supply operations. This central view can be updated easily without having to purchase software or hardware. It makes the supply chain flexible and scalable. Organizations can use real-time intelligence to plan better and coordinate with vendors to maximize their business's performance. It's a win/win situation for everyone involved. These are just some of the benefits you get from integrating your supply chain.
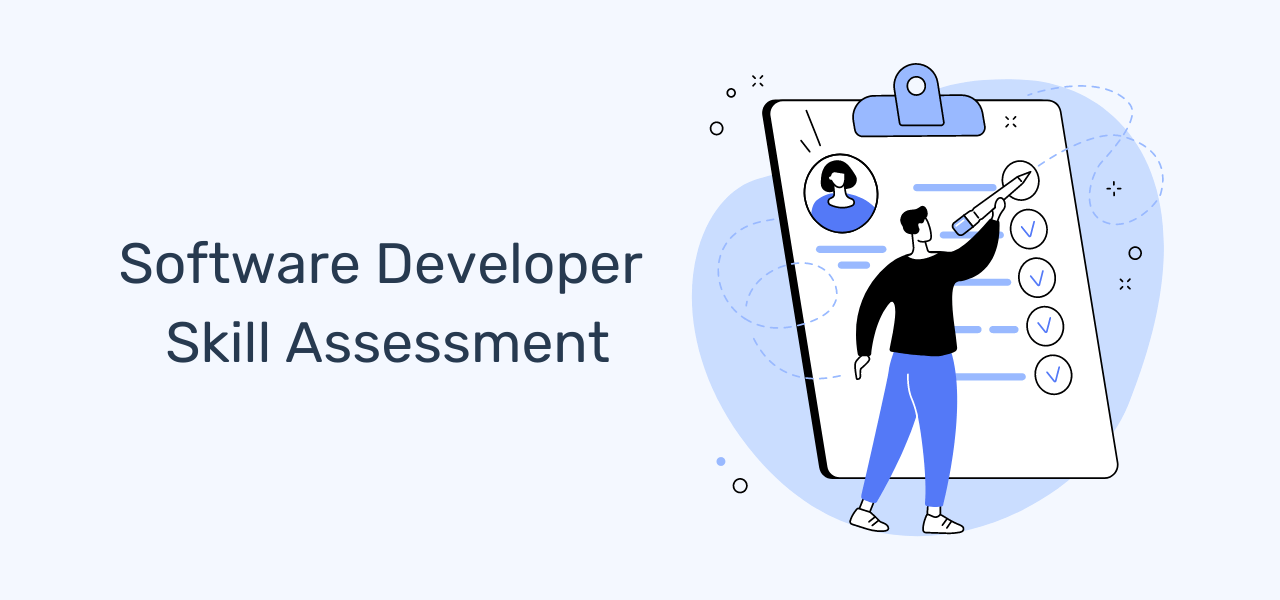
It allows for quick product design, manufacturing, and assembly
Manufacturers now have the ability to design and make complete products in half the time it used take with integrated supply chain administration. This trend can reduce material wastage and warehouse costs. Also, on-demand production offers better customer services. The only downside is the steep learning curve. It is possible to create products using only a few hours of new materials and hardware. It can also enhance the product's quality.
FAQ
What's the difference between a program and a project?
A project is temporary; a program is permanent.
A project usually has a specific goal and deadline.
It is often done in a team that reports to another.
A program often has a set goals and objectives.
It is usually done by one person.
What are the steps involved in making a decision in management?
Managers have to make complex decisions. It involves many factors, such as analysis and strategy, planning, execution, measurement, evaluation, feedback etc.
The key thing to remember when managing people is that they are human beings just as you are and therefore make mistakes. As such, there are always opportunities for improvement, especially when you put in the effort to improve yourself.
We explain in this video how the Management decision-making process works. We'll discuss the different types and reasons they are important. Managers should also know how to navigate them. You'll learn about the following topics:
What are the main styles of management?
There are three main management styles: participative, laissez-faire and authoritarian. Each style has strengths and flaws. What style do you prefer? Why?
Authority - The leader is the one who sets the direction and expects everyone in the organization to follow it. This style is best when the organization has a large and stable workforce.
Laissez faire - Each individual can decide for himself/herself. This style works best when an organization is small and dynamic.
Participative: The leader listens to everyone's ideas and suggestions. This style works best in smaller organizations where everyone feels valued.
How can we create a culture of success in our company?
A successful company culture is one that makes people feel valued and respected.
It's built on three fundamental principles:
-
Everybody has something to offer.
-
People are treated fairly
-
It is possible to have mutual respect between groups and individuals
These values are reflected by the way people behave. They will show consideration and courtesy to others.
They will listen to other people's opinions respectfully.
And they will encourage others to share ideas and feelings.
A company culture encourages collaboration and communication.
People feel safe to voice their opinions without fear of reprisal.
They are aware that mistakes can be accepted if they are treated honestly.
The company culture promotes honesty, integrity, and fairness.
Everyone understands that the truth is always best.
Everyone understands there are rules that they must follow.
And no one expects special treatment or favors.
What is the difference of leadership and management?
Leadership is about being a leader. Management is all about controlling others.
A leader inspires followers while a manager directs workers.
Leaders inspire people to achieve success. Managers keep their workers focused.
A leader develops people; a manager manages people.
What is TQM and how can it help you?
The industrial revolution led to the birth and growth of the quality movement. Manufacturing companies realized they couldn't compete solely on price. If they wanted to stay competitive, they needed to improve their quality and efficiency.
Management developed Total Quality Management to address the need for improvement. It focused on all aspects of an organisation's performance. It involved continuous improvement, employee participation, and customer satisfaction.
Six Sigma is so popular.
Six Sigma is easy and can deliver significant results. It can also be used to help companies identify and focus on the most important aspects of their business.
Statistics
- Your choice in Step 5 may very likely be the same or similar to the alternative you placed at the top of your list at the end of Step 4. (umassd.edu)
- The BLS says that financial services jobs like banking are expected to grow 4% by 2030, about as fast as the national average. (wgu.edu)
- Our program is 100% engineered for your success. (online.uc.edu)
- The average salary for financial advisors in 2021 is around $60,000 per year, with the top 10% of the profession making more than $111,000 per year. (wgu.edu)
- As of 2020, personal bankers or tellers make an average of $32,620 per year, according to the BLS. (wgu.edu)
External Links
How To
How do I get my Six Sigma License?
Six Sigma is an effective quality management tool that can improve processes and increase productivity. Six Sigma is a method that helps companies get consistent results from their operations. The name comes from the first two letters of the Greek word "sigmas" which mean "six." This process was developed at Motorola in 1986. Motorola realized that standardizing manufacturing processes was necessary to make products more efficient and less expensive. The many people involved in manufacturing had caused problems with consistency. They decided to use statistical tools like control charts and Pareto analysis to solve the problem. These techniques would be applied to every aspect of the operation. They would then be able make improvements where needed. To get Six Sigma certified, there are three key steps. Finding out if the certification is available for you is the first step. You will need classes to pass before you can begin taking tests. Once you pass those classes, the test will begin. It is important to review everything that you have learned in class. Then, you'll be ready to take the test. You will be certified if you pass the test. Final, your certifications can be added to you resume.