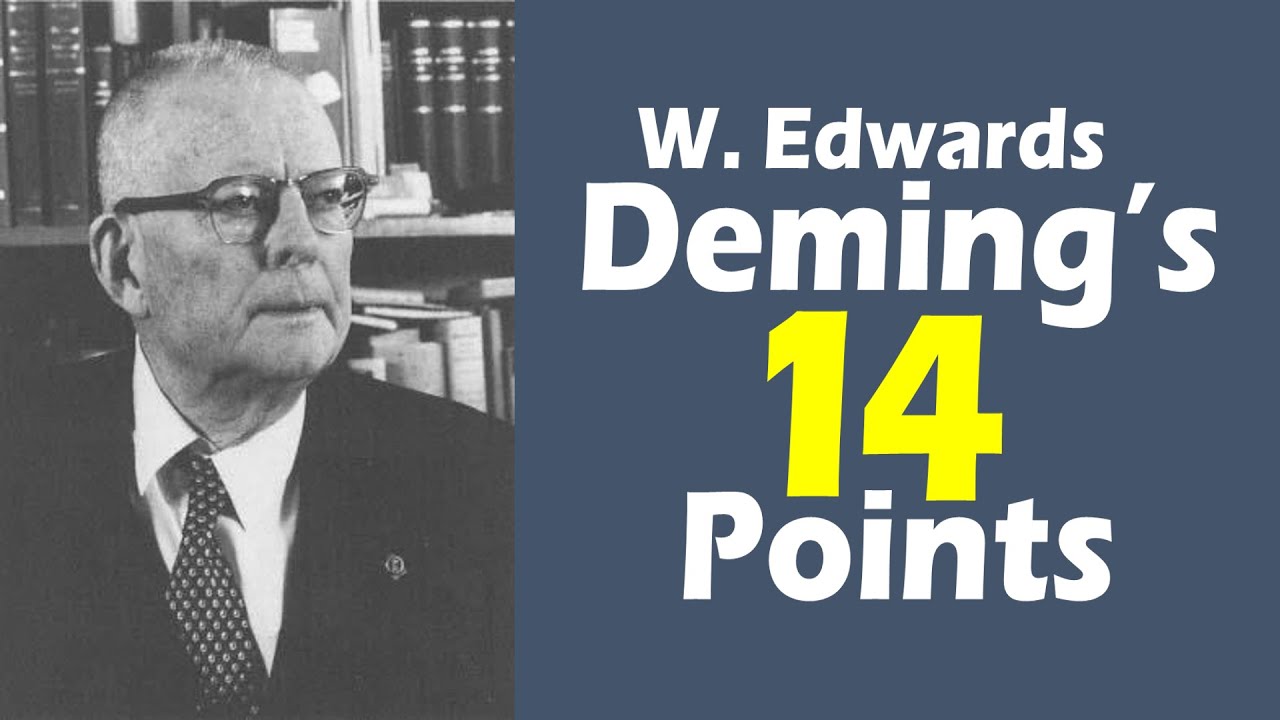
The Dynamics Supply Chain Management solution has comprehensive functionality for managing product lifecycles. It also allows companies to configure products for process or discrete manufacturing, evaluate suppliers, match items with suppliers and submit RFQs. The solution also offers tools to manage inventory and inventories. It gives you a complete overview of stock and production status. This software makes it easy to manage and create orders from one place.
Dynamics 365
The purpose of Dynamics 365 Supply Chain Management (SCM) is to improve the operational efficiency and quality of the end product for your company. It integrates sales and purchasing processes, logistics, warehouse management, and warehouse administration. It provides smart insights into every transaction. Dynamics 365 SMCM is a distributed management tool that can handle many other functions such as asset management cost management master planning product information management service management transportation and service management.
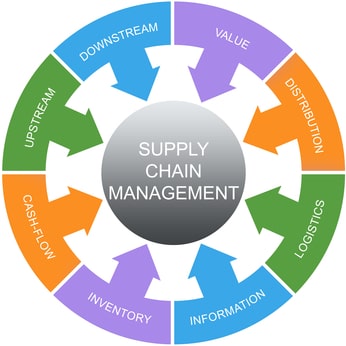
In addition, the solution has an advanced inventory management tool that automates the process for every step in the manufacturing process. It also enables you to optimize warehouse space and streamline field service operations. It also has machine learning capabilities that allow it to recommend better inventory management methods. Your company will enjoy optimal inventory management and minimize downtime. It also helps to manage the lifecycle of finished goods and material efficiently, and increases the productivity of your employees.
Dynamics 365 Planning Optimization Add-in
If you are using Microsoft Dynamics 365 to run your supply chain, you may be interested in the new planning optimization add-in. This powerful feature will help you plan and manage inventory and transportation. It allows you analyze operations with key performance indicators (KPIs). It also facilitates inventory stock adjustments and capacity restrictions. In addition, it can automate field service operations. This powerful planning optimization tool can be downloaded here.
The new add-in makes master planning even easier. You can now comply with multiple national standards for inventory accounting in a single system. This add-in enables real-time inventory control by simultaneously gathering data from multiple origin points. Global supply chain efficiency is dependent on inventory visibility in this constantly changing world. This add-in allows you to concentrate your company on mission-critical manufacturing operations.
Dynamics 365 Dynamics 365 Dynamics 365 Dynamics 365 Dynamics 365 Dynamics 365 Dynamics 365 Dynamics 365 Dynamics 365 Dynamics 365 Dynamics 370 Dynamics 365 Dynamics 365 Dynamics 365 Dynamics 365 Dynamics 365 Dynamics 365 Dynamics 365 Dynamics 365 Dynamics 365 Dynamics...
Microsoft Dynamics is the latest version their business management software. It's the next generation in their supply chain management solutions. This cloud-based solution includes all the features of Dynamics AX. It also helps you improve operational efficiency and improve the quality of your end product. It is possible to integrate existing systems with the software, allowing you to automate deliveries, inventory management, cost management, as well as cost management.
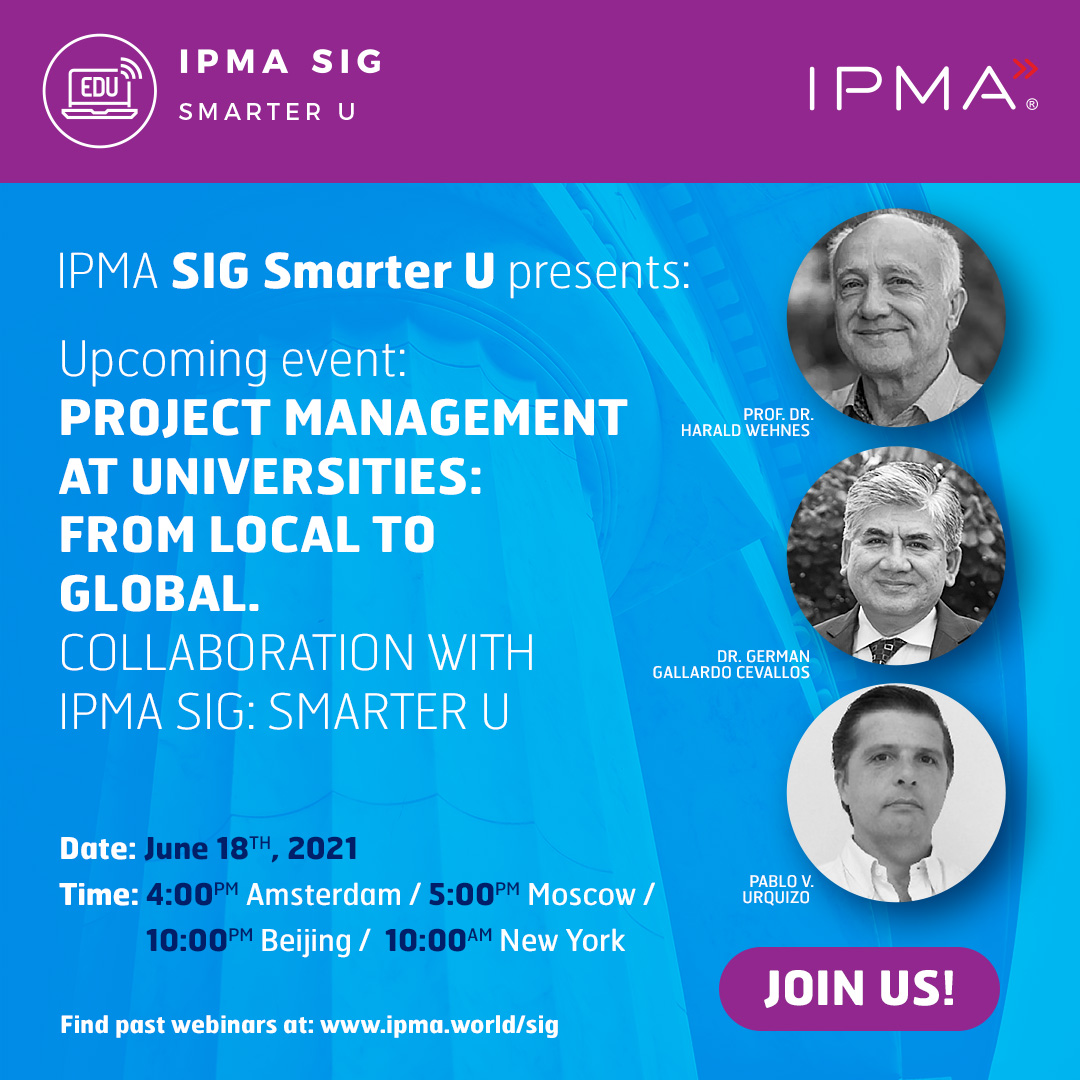
This solution integrates all functions of the supply chain into a single system. It includes purchasing, inventory management, and transportation management. It gives real-time information to enhance planning and decision-making. It supports the accounting conservatism principle, and offers new reporting through Power BI. The wizard provides a step-by–step process for setting up the program. It gives you near-real-time visibility to inventories and validates fulfillment dates with an ATP check. It helps you allocate stocks based on demand and profitability, allowing you to make strategic decisions that benefit your business. You can also automate field service operations to make it easier for you to get up-and-running faster.
FAQ
How can a manager improve his/her managerial skills?
Good management skills are essential for success.
Managers must constantly monitor the performance of their subordinates.
You must act quickly if you notice that your subordinate isn’t performing to their standards.
It is important to be able identify areas that need improvement and what can be done to improve them.
What's the difference between Six Sigma and TQM?
The main difference between these two quality-management tools is that six-sigma concentrates on eliminating defects while total QM (TQM), focuses upon improving processes and reducing expenses.
Six Sigma is an approach for continuous improvement. It emphasizes the elimination or minimization of defects through statistical methods such control charts and p charts.
This method seeks to decrease variation in product output. This is done by identifying and correcting the root causes of problems.
Total quality management is the measurement and monitoring of all aspects within an organization. Training employees is also part of total quality management.
It is frequently used as an approach to increasing productivity.
What is TQM, exactly?
The quality movement was born during the industrial revolution when manufacturing companies realized they could not compete on price alone. If they wanted to stay competitive, they needed to improve their quality and efficiency.
To address this need for improvement management created Total Quality Management (TQM) which aimed to improve all aspects of an organization's performance. It included continuous improvement, employee involvement and customer satisfaction.
Statistics
- The BLS says that financial services jobs like banking are expected to grow 4% by 2030, about as fast as the national average. (wgu.edu)
- Our program is 100% engineered for your success. (online.uc.edu)
- Hire the top business lawyers and save up to 60% on legal fees (upcounsel.com)
- As of 2020, personal bankers or tellers make an average of $32,620 per year, according to the BLS. (wgu.edu)
- The average salary for financial advisors in 2021 is around $60,000 per year, with the top 10% of the profession making more than $111,000 per year. (wgu.edu)
External Links
How To
How do I get my Six Sigma certification?
Six Sigma is a quality management tool to improve processes and increase efficiency. It's a system that allows companies to get consistent results from operations. The name comes from the first two letters of the Greek word "sigmas" which mean "six." Motorola developed this process in 1986. Motorola realized they needed to standardize the manufacturing processes to produce products faster and cheaper. The many people involved in manufacturing had caused problems with consistency. To solve this problem, they decided to use statistical tools such as control charts and Pareto analysis. They would then apply these techniques to all aspects of their operation. This would allow them to make any necessary changes. When you are trying to obtain your Six Sigma certification, there are three steps. Finding out if the certification is available for you is the first step. Before you take any exams, you'll need to take some classes. After you have passed the classes, you can start taking the exams. You'll need to go back and review all the information you received in class. Then, you'll be ready to take the test. If you pass, your certification will be granted. And finally, you'll be able to add your certifications to your resume.