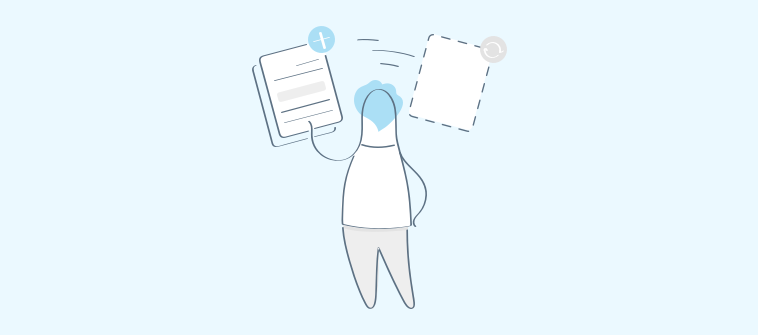
An online degree in engineering management can be obtained. A BSc in engineering management can be obtained online. It is necessary to take ME, EE, CS courses. Capstone classes are taken two semesters back-to-back. A capstone project is also required. It is necessary to meet some requirements in order to be able to receive your online degree. These requirements will help you determine whether the program is right to you.
BS in engineering management
Asu offers a Bachelor of Science in Engineering Management, which gives students advanced knowledge in engineering management. It also helps them develop leadership skills. The program combines core business courses and coursework in engineering and administration. These include organizational behavior, finance, managerial accounting, and financial management. Graduates of this program can be prepared to work in a variety of managerial roles including quality control and production managers as well as technicians in industrial engineering. The flexibility and affordability of the program, as well as its easy online learning options, have made it a very popular option for engineering students.
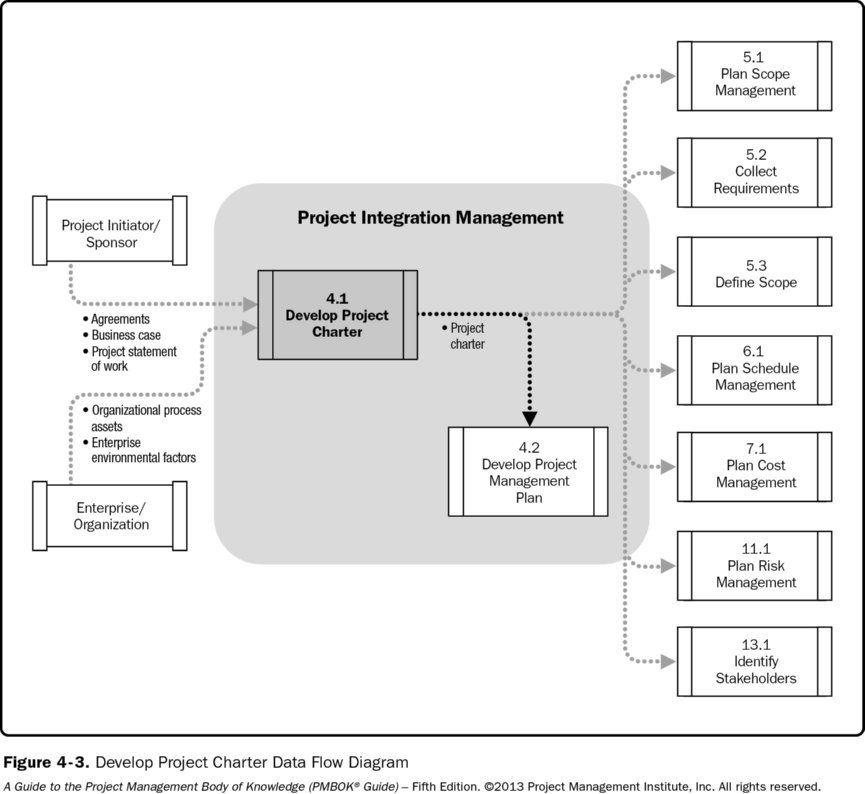
While the BS in Engineering Management degree emphasizes management and analytical principles, it also emphasizes technical engineering expertise. Students will learn how these two concepts can be integrated and applied to organizational goals. Flexible, students can complete their degree online and continue to work in their current job. This flexibility allows students to explore different career paths beyond their expertise. If you're looking to build a career that combines your passion for technology and management, this is an excellent program for you.
Online programs in engineering management
Online engineering management programs will help you achieve the education you desire, regardless of whether you are looking for a job or advancement in your career. These online degrees give you the skills to lead the day-today operations of an engineering business. Although you may not have an engineering degree you can still pursue this career by earning a master’s in civil engineering and a specialization on engineering management.
A Master's program in Engineering Management is offered online by the University of Maryland's A. James Clark School of Engineering. This program of thirty credits prepares engineers to hold executive-level jobs. It integrates management principles and sound engineering principles. It is the first college-level engineering management program to earn accreditation from the Project Management Institute Global Accreditation Center. Drexel University's online Master of Engineering Management degree program requires only one or two classes per week. Depending on your personal schedule, your program can be completed within two to four years.
Engineering management programs require entry requirements
The following criteria are required to be eligible for engineering management programs. A baccalaureate degree is required in technical disciplines, including relevant courses in programming and statistics. You should also have a grade point average of 3.0 or higher in the last two years of undergraduate study. You will also need to complete nine credits in electives, including Problems in Engineering Management.
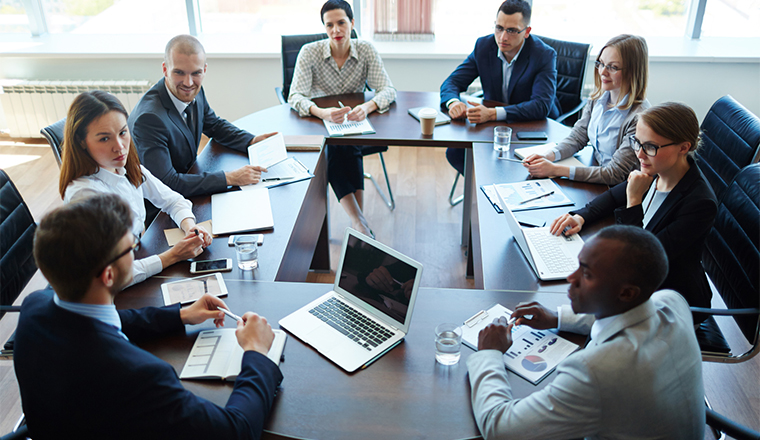
Admission to the program requires a bachelor's degree in science-related fields such as engineering, accounting, economics or economics. The applicant must have some experience in the workplace and some knowledge about financial and business principles. It is possible to also learn fundamental economic theories and apply them in an engineering context, depending on what school you go to. It is possible that you will need to take one or more prerequisite courses, depending on the school to which you apply. It is a good idea to apply for as many as eight programs before deciding on one.
FAQ
How do we build a culture that is successful in our company?
A company culture that values and respects its employees is a successful one.
It is founded on three basic principles:
-
Everyone has something valuable to contribute
-
People are treated fairly
-
It is possible to have mutual respect between groups and individuals
These values are reflected in the way people behave. They will treat others with consideration and courtesy.
They will listen to other people's opinions respectfully.
They encourage others to express their feelings and ideas.
In addition, the company culture encourages open communication and collaboration.
People feel safe to voice their opinions without fear of reprisal.
They understand that errors will be tolerated as long they are corrected honestly.
Finally, the company culture encourages honesty as well as integrity.
Everyone knows that they must always tell truth.
Everyone recognizes that rules and regulations are important to follow.
People don't expect special treatment or favors.
What is TQM exactly?
The industrial revolution was when companies realized that they couldn't compete on price alone. This is what sparked the quality movement. To remain competitive, they had to improve quality as well as efficiency.
To address this need for improvement management created Total Quality Management (TQM) which aimed to improve all aspects of an organization's performance. It included continual improvement processes, employee involvement, customer satisfaction, and customer satisfaction.
What is the difference in Six Sigma and TQM?
The major difference between the two tools for quality management is that six Sigma focuses on eliminating defect while total quality control (TQM), on improving processes and decreasing costs.
Six Sigma can be described as a strategy for continuous improvement. It emphasizes the elimination and improvement of defects using statistical methods, such as control charts, P-charts and Pareto analysis.
This method has the goal to reduce variation of product output. This is done by identifying root causes and rectifying them.
Total quality management is the measurement and monitoring of all aspects within an organization. This includes training employees to improve their performance.
It is commonly used as a strategy for increasing productivity.
Statistics
- Your choice in Step 5 may very likely be the same or similar to the alternative you placed at the top of your list at the end of Step 4. (umassd.edu)
- Our program is 100% engineered for your success. (online.uc.edu)
- The profession is expected to grow 7% by 2028, a bit faster than the national average. (wgu.edu)
- The average salary for financial advisors in 2021 is around $60,000 per year, with the top 10% of the profession making more than $111,000 per year. (wgu.edu)
- UpCounsel accepts only the top 5 percent of lawyers on its site. (upcounsel.com)
External Links
How To
How do I do the Kaizen Method?
Kaizen means continuous improvement. The Japanese philosophy emphasizes small, incremental improvements to achieve continuous improvement. This term was created by Toyota Motor Corporation in 1950. It's a process where people work together to improve their processes continuously.
Kaizen is one method that Lean Manufacturing uses to its greatest advantage. Kaizen is a concept where employees in charge of the production line are required to spot problems during the manufacturing process before they become major issues. This increases the quality of products and reduces the cost.
The main idea behind kaizen is to make every worker aware of what happens around him/her. To prevent problems from happening, any problem should be addressed immediately. It is important that employees report any problems they see while on the job to their managers.
There are some basic principles that we follow when doing kaizen. The end product is always our starting point and we work toward the beginning. We can improve the factory by first fixing the machines that make it. Then, we fix the machines that produce components and then the ones that produce raw materials. And finally, we fix the workers who work directly with those machines.
This method, called 'kaizen', focuses on improving each and every step of the process. After we're done with the factory, it's time to go back and fix the problem.
You need to know how to measure the effectiveness of kaizen within your business. There are several ways that you can tell if your kaizen system is working. One of these ways is to check the number of defects found on the finished products. Another way is to see how much productivity has increased since implementing kaizen.
A good way to determine whether kaizen has been implemented is to ask why. It was because of the law, or simply because you wanted to save some money. You really believed it would make you successful?
Let's say you answered yes or all of these questions. Congratulations! You're now ready to get started with kaizen.