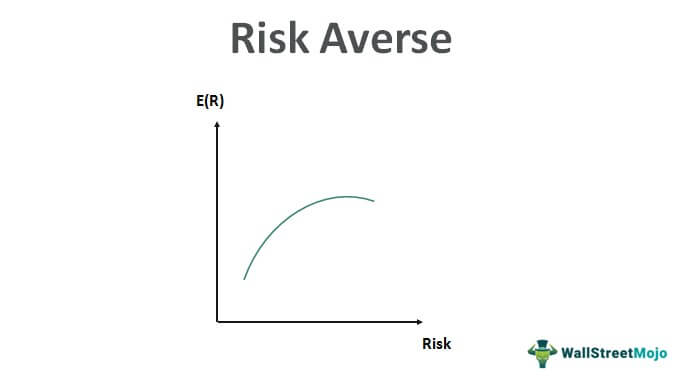
Management involves taking decisions and managing tasks to achieve a goal. This article will explain how to manage various tasks. It includes creating and maintaining an environment that encourages others to reach their goals. Managemnet is the act of getting things done with people who aren't necessarily organized into groups. Here are some of the common tasks that people manage. These tasks can be:
Management is the coordination or administration of tasks that lead to a goal.
The definition of management is different depending on what industry you work in and where you live. Management involves setting the strategy for an organisation and coordinating the efforts by staff. It also refers a staff's seniority. Management includes also the management of resources. Despite their many differences, there are common traits. These are some examples for management roles:
It involves creating an environment within the company.
The environment within a business organization is determined by seven things. These include the value system of the organization, its mission, and objectives, the organizational structure, the style of top management, the quality of human resources, labour unions, and the physical resources of the organization. A firm's inner environment is also important in determining its decision-making. A culture that fosters innovation is essential to the success of an organization.
This involves convincing someone or something to achieve a desired result.
Persuasion refers to the act of convincing someone or something to do something. Persuasion can be hard, but it is possible in certain situations. Here are some tips that will help you convince others. Try them out:
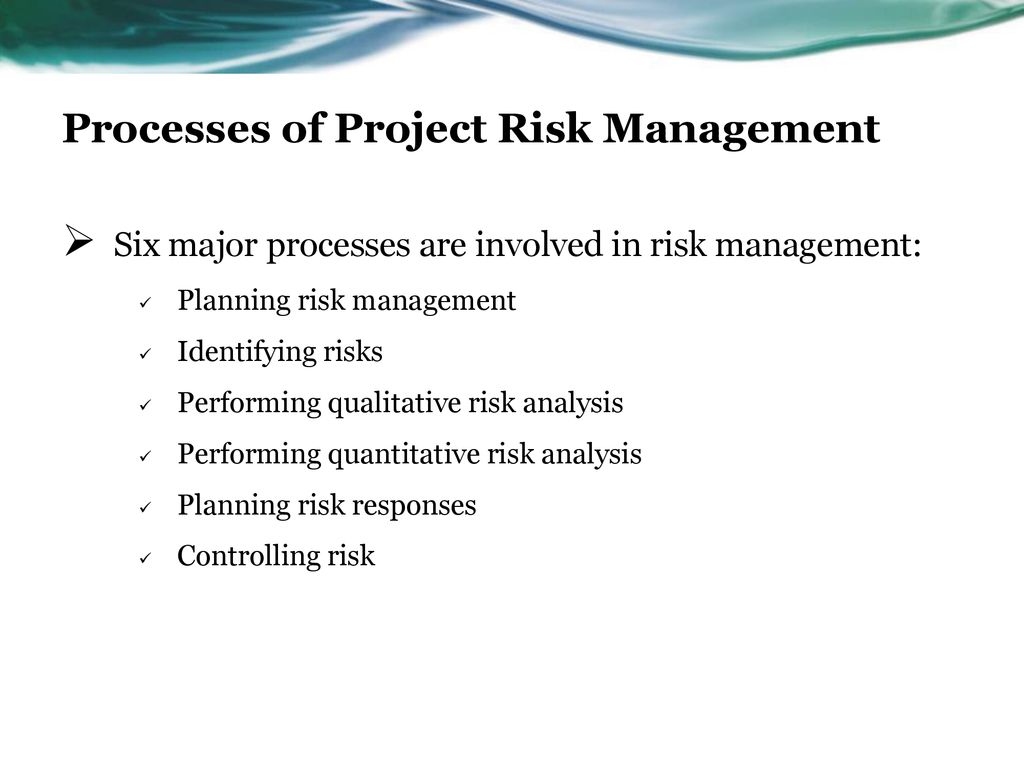
It involves working together with informal groups to get things done
Management is an art of getting things done through and with the people involved in a group. Informally organized groups make up the backbone and formal organizations the brains. While the former helps companies maintain their standard production methods, the latter can be used to address unexpected issues. This theory is based on the American organizational theorist, Harold Koontz.
FAQ
What is the difference between a project and a program?
A program is permanent while a project can be temporary.
A project typically has a defined goal and deadline.
It is often carried out by a team of people who report back to someone else.
A program will usually have a set number of goals and objectives.
It is often implemented by one person.
What is the difference between leadership and management?
Leadership is all about influencing others. Management is about controlling others.
Leaders inspire followers, while managers direct workers.
A leader inspires others to succeed, while a manager helps workers stay on task.
A leader develops people; a manager manages people.
What are some common mistakes managers make?
Sometimes managers make their job harder than they need to.
They may not assign enough responsibilities to staff members and provide them with inadequate support.
Additionally, many managers lack communication skills that are necessary to motivate and direct their teams.
Managers can set unrealistic expectations for their employees.
Some managers may try to solve every problem themselves instead of delegating responsibility to others.
Statistics
- Hire the top business lawyers and save up to 60% on legal fees (upcounsel.com)
- The BLS says that financial services jobs like banking are expected to grow 4% by 2030, about as fast as the national average. (wgu.edu)
- The average salary for financial advisors in 2021 is around $60,000 per year, with the top 10% of the profession making more than $111,000 per year. (wgu.edu)
- Our program is 100% engineered for your success. (online.uc.edu)
- The profession is expected to grow 7% by 2028, a bit faster than the national average. (wgu.edu)
External Links
How To
What is Lean Manufacturing?
Lean Manufacturing processes are used to reduce waste and improve efficiency through structured methods. They were developed in Japan by Toyota Motor Corporation (in the 1980s). The aim was to produce better quality products at lower costs. Lean manufacturing focuses on eliminating unnecessary steps and activities from the production process. It includes five main elements: pull systems (continuous improvement), continuous improvement (just-in-time), kaizen (5S), and continuous change (continuous changes). It is a system that produces only the product the customer requests without additional work. Continuous improvement means continuously improving on existing processes. Just-intime refers the time components and materials arrive at the exact place where they are needed. Kaizen means continuous improvement, which is achieved by implementing small changes continuously. The 5S acronym stands for sort in order, shine standardize and maintain. To achieve the best results, these five elements must be used together.
The Lean Production System
Six key concepts are the basis of lean production:
-
Flow is about moving material and information as near as customers can.
-
Value stream mapping- This allows you to break down each step of a process and create a flowchart detailing the entire process.
-
Five S's, Sort, Set in Order, Shine. Standardize. and Sustain.
-
Kanban is a visual system that uses visual cues like stickers, colored tape or stickers to keep track and monitor inventory.
-
Theory of constraints: Identify bottlenecks and use lean tools such as kanban boards to eliminate them.
-
Just-intime - Order components and materials at your location right on the spot.
-
Continuous improvement - Make incremental improvements rather than overhauling the entire process.