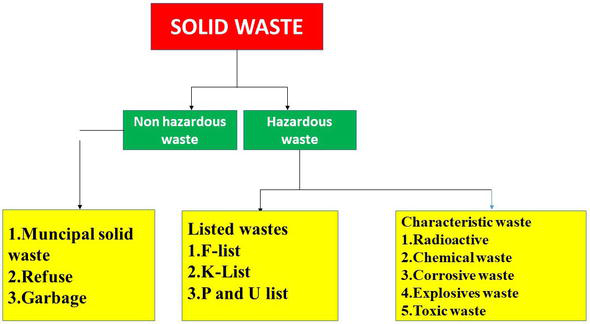
EASA has published good practice in relation to approval of design organisations. These practices provide technical explanations and clarifications on certain topics in the current standards. These practices are intended to be informational only and not as a guideline. The following sections offer a brief overview of the different design organisation approval models. The type of your business will influence the choice of the right model. A service-based business model, for example, is more appropriate for a service-based sector than a product one.
Model Holonic Enterprise
The holonic model of design organisation is a framework which allows for self-directed information, resource management, and collaboration in virtual global organisations. Arthur Koestler in 1968 described the selforganizing capabilities of biological and social systems. This is the basis of the holonic enterprise model for design organisation. Koestler created the term "holon", which describes a system that is both a self contained whole and a collaborative hierarchy.
Model of process-based organisation design
A process-based organizational design model is an effective tool for increasing the performance of an organisation. The three-part approach to designing an organisation is based upon three key components: the people (systems and process), the process (process) and the system (process). The people component refers to designing the right people structure for a high-performing work environment. The systems function is responsible for ensuring that the organization runs smoothly. The process function is concerned with the processes that ensure the organisation's efficiency. The process paradigm is built on a horizontal view to business operations. It is the driving force behind a process-based organisational design model.
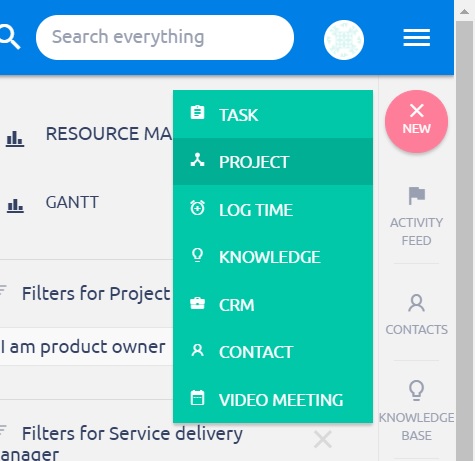
COVID
The World Design Organization is mobilizing the design community for the COVID-19 crisis. In partnership with Design for America and IBM Corporate Service Corps, the organization has distilled the 180 challenge statements from around the world into seven large themes that designers can tackle to make a difference. These are three key points of action:
COVID-19
The COVID-19 Design Challenge was launched by Design for America and IBM Design with a focus in global health. With the help of this global initiative, designers and companies around the world were able to mobilize and create designs that would address COVID-19's five pressing challenges. Participants created projects that could prevent or reduce the severity of the disease.
COVID-20
COVID-20, the next evolution in design organisation, is being offered as the solution to unprecedented global challenges. Organizations can design for the future to be able to quickly respond to rising costs while also leveraging advanced digital operations that allow them to thrive in times of low prices. Meanwhile, cyber attacks continue to threaten organizations, municipalities, state and federal governments, and companies of all sizes. The good news is that technology today can enhance these defenses. Learn how to use this new paradigm within your organization.
COVID-21
To ensure safety and efficiency, the next generation of aviation requires innovative and collaborative design methods. In response to this challenge, CAE is developing a new design organisation, COVID-21. The latest research will inform the new organization, which will make aviation and airports safer. It will also be able to assist companies and governments in creating plans for the next. Its goal is to foster global cooperation and aviation resilience and sustainability.
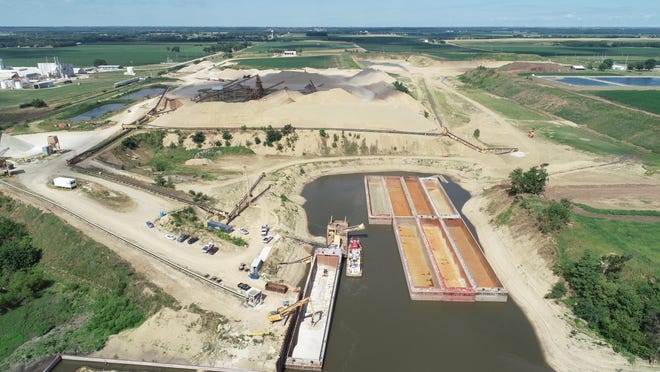
COVID-22
A new capitation payment model is coming to health centers in the U.S. in 2022. This model encourages physicians to spend more time talking to patients and to improve their health. Blue Cross Blue Shield of North Carolina's (BCBSNC), is supporting community health centers as the new payment model is implemented. These include faster payments and proactive measures to help doctors navigate the new system. These steps will increase patient access and decrease the burden on providers by reducing the cost of insurance.
COVID-23
The Global Youth Residibility Fund was launched by the international youth fund. This fund funds national and regional youth organisations in support of projects that improve human rights, create livelihoods, and provide reliable information. The fund's Project DAAM initiative stands for research advocacy and capacity. The fund provides grants for research on the impact of COVID-19 and vulnerable groups.
COVID-24
Organisations should be mindful of their leadership models, operational frameworks, and organizational strategies when designing COVID-19. Deloitte created a website to support this anti-corruption initiative. Implementing the COVID-19 method can help organisations ensure safety and health at work and in their environment. COVID-19 offers a chance to raise communication levels, create a culture of resilience and health, and improve communications.
FAQ
Which kind of people use Six Sigma
People who have worked with statistics and operations research will usually be familiar with the concepts behind six sigma. But anyone can benefit from it.
This requires a lot of dedication, so only people with great leadership skills can make the effort to implement it.
What's the difference between leadership & management?
Leadership is about being a leader. Management is about controlling others.
Leaders inspire followers, while managers direct workers.
A leader motivates people and keeps them on task.
A leader develops people; a manager manages people.
What is TQM exactly?
When manufacturing companies realized that price was not enough to compete, the industrial revolution brought about the quality movement. They needed to improve quality and efficiency if they were going to remain competitive.
Management responded to the need to improve, and developed Total Quality Management (TQM). This focused on improving every aspect of an organization’s performance. It included continual improvement processes, employee involvement, customer satisfaction, and customer satisfaction.
Statistics
- Your choice in Step 5 may very likely be the same or similar to the alternative you placed at the top of your list at the end of Step 4. (umassd.edu)
- UpCounsel accepts only the top 5 percent of lawyers on its site. (upcounsel.com)
- The average salary for financial advisors in 2021 is around $60,000 per year, with the top 10% of the profession making more than $111,000 per year. (wgu.edu)
- The profession is expected to grow 7% by 2028, a bit faster than the national average. (wgu.edu)
- Our program is 100% engineered for your success. (online.uc.edu)
External Links
How To
What is Lean Manufacturing?
Lean Manufacturing processes are used to reduce waste and improve efficiency through structured methods. They were created in Japan by Toyota Motor Corporation during the 1980s. The main goal was to produce products at lower costs while maintaining quality. Lean manufacturing eliminates unnecessary steps and activities from a production process. It has five components: continuous improvement and pull systems; just-in time; continuous change; and kaizen (continuous innovation). Pull systems allow customers to get exactly what they want without having to do extra work. Continuous improvement refers to continuously improving existing processes. Just-in–time refers when components or materials are delivered immediately to their intended destination. Kaizen is continuous improvement. This can be achieved by making small, incremental changes every day. Finally, 5S stands for sort, set in order, shine, standardize, and sustain. These five elements can be combined to achieve the best possible results.
Lean Production System
Six key concepts are the basis of lean production:
-
Flow: The goal is to move material and information as close as possible from customers.
-
Value stream mapping- This allows you to break down each step of a process and create a flowchart detailing the entire process.
-
Five S's – Sort, Put In Order Shine, Standardize and Sustain
-
Kanban – visual signals like colored tape, stickers or other visual cues are used to keep track inventory.
-
Theory of constraints - identify bottlenecks in the process and eliminate them using lean tools like kanban boards;
-
Just-intime - Order components and materials at your location right on the spot.
-
Continuous improvement - incremental improvements are made to the process, not a complete overhaul.