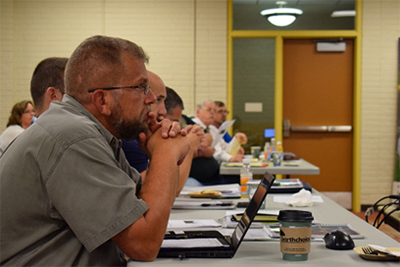
Employees should be included in the change process. Ask employees to give input on the new process or policy. Employees should be consulted about important decisions that affect their department or role. The change process provides employees with time to analyze and consider new ideas. Participation by employees in the change process will make them more open to the possibilities. Participating in the design and implementation of the policy is a great way to get them involved. This article will cover the four phases of employee change.
There are four phases to employee change
Separation is the first stage of the change process. This happens between 0 and 3 months before the employee leaves the company. The employee can initiate the process, or the company may do it. The company's timing will differ from one company to the next. However, most companies require employees not to inform their employers less than two weeks before they plan to leave. This allows the company to prepare for the worst.
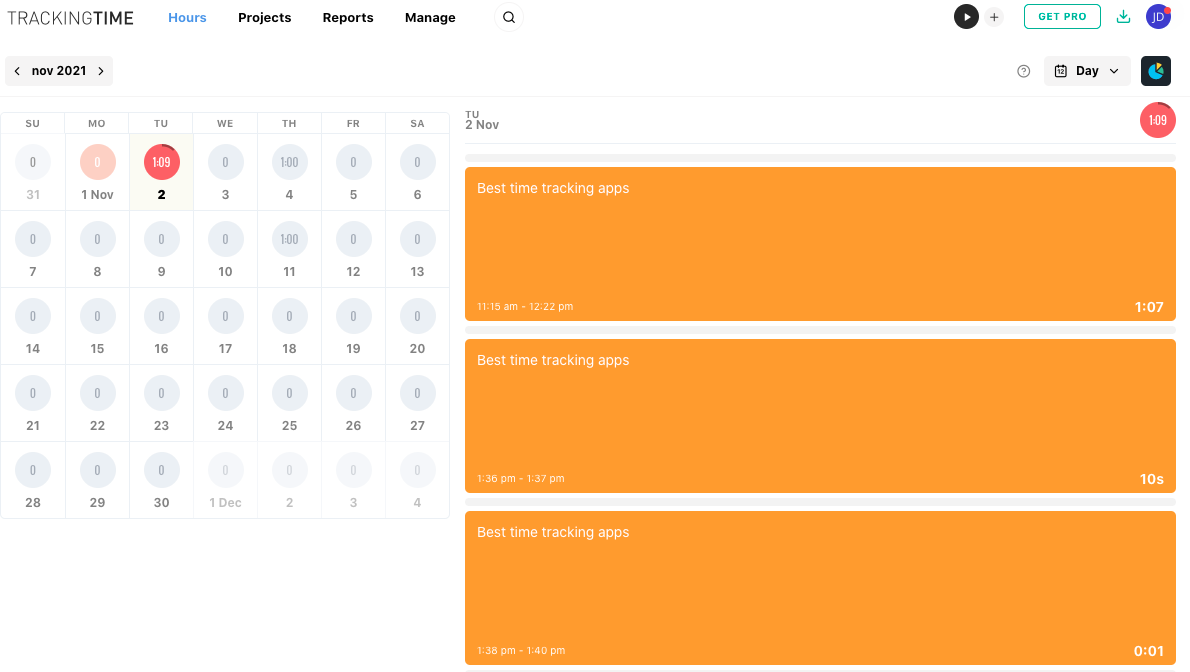
Communication
A key part of any successful change management process is communication. Communicating the changes to employees in a way that encourages them to adopt new working methods is crucial. Understanding the needs of your employees and the changes must be the basis for communication. It should be a two way process, with frequent and consistent communication. In addition, you should make sure that you communicate with different audiences to make sure that you reach everyone.
Empowerment
The use of technology and team-building activities can help to develop employees and foster engagement. Your employees will feel more connected and appreciated by their coworkers. This will create a better working environment. You can also create mentoring circles and idea exchanges to help employees connect with other departments. Employees who feel empowered are more likely to take initiative in solving problems and contribute to the success of the company. How do you encourage employees to get involved?
Up-front communication
Effective change management starts with open communication. Explain to employees the changes and how they will affect them. Employees should be made aware of the changes so that they can embrace them. Communication of the changes should be clear and simple to avoid any misunderstandings. The right message should be sent to different audiences. If you are changing leadership, communicate this to all departments. Communicate with all departments when you're restructuring the company.
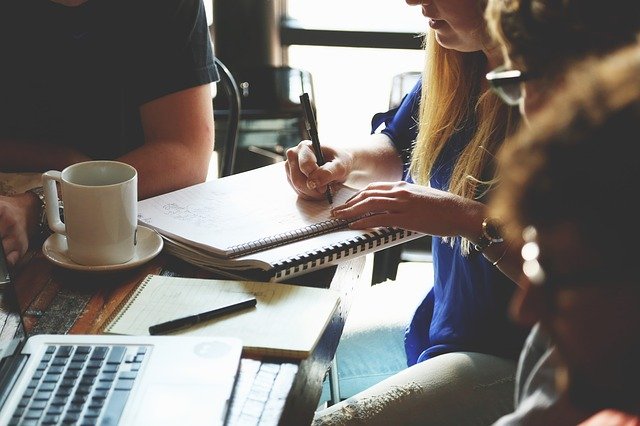
A supportive work environment
It is essential to create a supportive workplace environment that allows employees to make changes. This is key to employee satisfaction. It can also increase the bottom line. Employees are people, and motivating employees to achieve their goals can help them reach their full potential. Support, on the other hand, goes beyond motivation, and is more about the overall health of the employee. Therefore, it is important to understand the motivations of people and how they can be supported.
FAQ
What is Kaizen and how can it help you?
Kaizen, a Japanese term that means "continuous improvement," is a philosophy that encourages employees and other workers to continuously improve their work environment.
Kaizen is built on the belief that everyone should be able do their jobs well.
What does the term "project management” mean?
That is the management of all activities associated with a project.
Our services include the definition of the scope, identifying requirements, preparing a budget, organizing project teams, scheduling work, monitoring progress and evaluating the results before closing the project.
What are the four main functions of management?
Management is responsible in planning, organizing and directing people and resources. This includes setting goals, developing policies and procedures, and creating procedures.
Management aids an organization in reaching its goals by providing direction and coordination, control, leadership motivation, supervision, training, evaluation, and leadership.
Management's four main functions are:
Planning - This is the process of deciding what should be done.
Organizing is the act of deciding how things should go.
Directing - Directing means getting people to follow instructions.
Controlling: Controlling refers to making sure that people do what they are supposed to.
What is the difference in a project and program?
A program is permanent while a project can be temporary.
A project usually has a specific goal and deadline.
It is usually done by a group that reports back to another person.
A program often has a set goals and objectives.
It is often done by one person.
What is the role of a manager in a company?
Each industry has a different role for a manager.
The manager oversees the day-to-day activities of a company.
He/she makes sure that the company meets its financial obligations, and that it produces goods or services that customers desire.
He/she ensures that employees follow the rules and regulations and adhere to quality standards.
He/she plans and oversees marketing campaigns.
What is Six Sigma?
It's an approach to quality improvement that emphasizes customer service and continuous learning. The objective is to eliminate all defects through statistical methods.
Motorola developed Six Sigma in 1986 to help improve its manufacturing processes.
It was quickly adopted by the industry and many companies are now using six-sigma to improve product design, production, delivery, customer service, and product design.
What is TQM?
When manufacturing companies realized that price was not enough to compete, the industrial revolution brought about the quality movement. They needed to improve quality and efficiency if they were going to remain competitive.
Management responded to the need to improve, and developed Total Quality Management (TQM). This focused on improving every aspect of an organization’s performance. It involved continuous improvement, employee participation, and customer satisfaction.
Statistics
- Hire the top business lawyers and save up to 60% on legal fees (upcounsel.com)
- The BLS says that financial services jobs like banking are expected to grow 4% by 2030, about as fast as the national average. (wgu.edu)
- Our program is 100% engineered for your success. (online.uc.edu)
- This field is expected to grow about 7% by 2028, a bit faster than the national average for job growth. (wgu.edu)
- The profession is expected to grow 7% by 2028, a bit faster than the national average. (wgu.edu)
External Links
How To
How can you use the Kaizen method?
Kaizen means continuous improvement. The Japanese philosophy emphasizes small, incremental improvements to achieve continuous improvement. This term was created by Toyota Motor Corporation in 1950. It's a team effort to continuously improve processes.
Kaizen is one method that Lean Manufacturing uses to its greatest advantage. Employees responsible for the production line should identify potential problems in the manufacturing process and work together to resolve them. This will increase the quality and decrease the cost of the products.
Kaizen is a way to raise awareness about what's happening around you. To prevent problems from happening, any problem should be addressed immediately. Report any problem you see at work to your manager.
Kaizen follows a set of principles. When working with kaizen, we always start with the end result and move towards the beginning. We can improve the factory by first fixing the machines that make it. We then fix the machines producing components, and the machines producing raw materials. We then fix the workers that work with those machines.
This is why it's called "kaizen" because it works step-by-step to improve everything. After we're done with the factory, it's time to go back and fix the problem.
To implement kaizen in your business, you need to find out how to measure its effectiveness. There are many methods to assess if kaizen works well. One method is to inspect the finished products for defects. Another way is to check how much productivity has grown since kaizen was implemented.
To determine if kaizen is effective, you should ask yourself why you chose to implement kaizen. Is it because the law required it or because you want to save money. Did you really believe that it would be a success factor?
Suppose you answered yes to any of these questions, congratulations! You're ready to start kaizen.