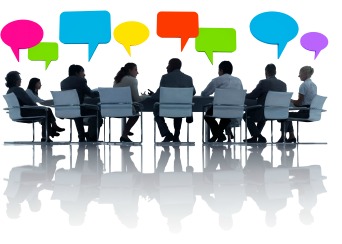
It is crucial for anyone who wants to move up in the construction management field. Accreditation ensures that the college or university meets the standards for the profession it prepares its graduates. Learn more about the different accreditations available, including ABET ACCE and Louisiana State University.
ABET accreditation assures that a college/university program meets professional standards.
The ABET accreditation process assures that a college program meets high quality standards and prepares graduates for success in their chosen field. ABET's voluntary peer reviewing process is highly regarded and adds value for technical programs.
A group of volunteers is responsible for ABET’s voluntary accreditation process. They represent industry, government, academia, private practice, and academia. The work of the team is focused on the program's quality, faculty, institutional support, and curriculum.
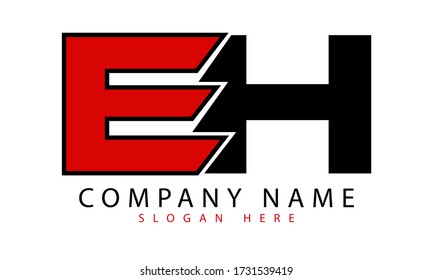
ACCE accreditation
ACCE accreditation of construction management programs is a valuable asset for potential students, employers, as well as employees. Accredited programs provide students with the skills and knowledge necessary to succeed in a construction management career. Employers can find quality workers easier with accreditation. Accredited programs can also foster leadership development, foster networking and keep abreast of construction trends.
American Council for Construction Education accredits both the Associate of Applied Science (ACCE) and the Bachelor of Science degrees in construction management. For the Bachelor's degree, you must complete a capstone course as well as internships within three year. Both programs require a minimum GPA (3.5) and a minimum GRE score (550). A few academic requirements are met and applicants may be allowed up to nine credits transfer from another institution. ACCE accreditation is rigorous. Accredited programs in construction management education must meet industry requirements.
ABET accreditation
Accreditation by ABET for construction management programs is a great way of ensuring quality education and to make sure that program content is reviewed by an independent governing body. Accreditation Board of Engineering and Technology (ABET) usually grants accreditation for construction management programs. The ABET accreditation process requires that programs adhere to certain standards. Accredited programs are designed to prepare students for technical fields and keep them up-to-date on the latest technology.
There may be multiple curricula at a school that is not accredited by the same ABET. Core courses may be shared between the programs in these cases. This may create competition for students and a risk of overextending resources.
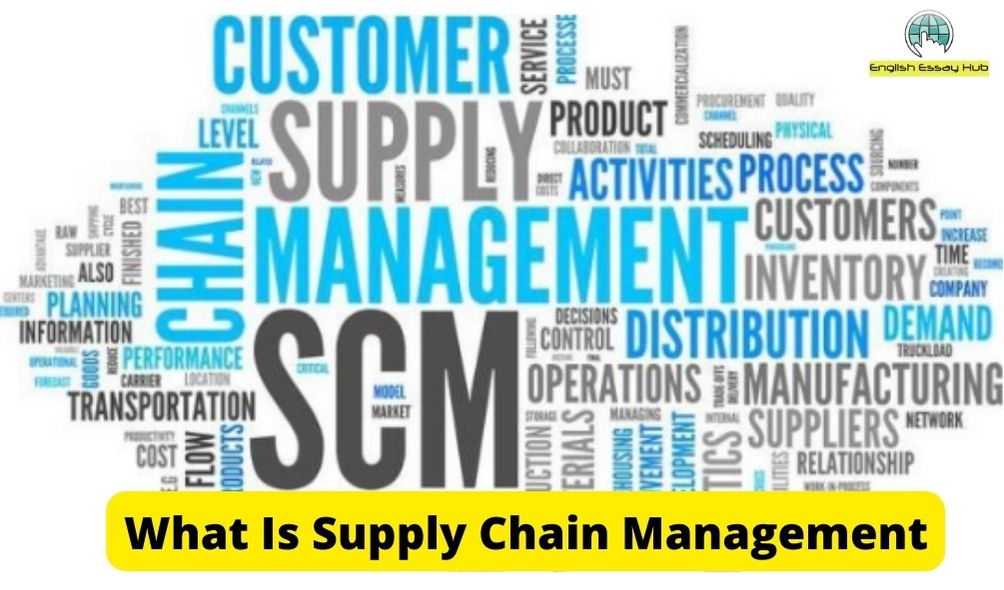
Louisiana State University accreditation
Louisiana State University gives you the training and skills necessary to manage a construction job. This program will teach you about project planning, design, construction delivery, and more. Additionally, you will learn how to incorporate sustainable practices in the construction process. This program is accredited by the American Council for Construction Education. It combines core courses in construction with leadership coursework to make you a competent construction manager.
Louisiana State University has an online Bachelor in Science in Construction Management. This program consists 6 CM courses which will give you a solid foundation in the field. After you complete the program requirements, you'll gain a unique perspective on the field.
FAQ
What is the difference between Six Sigma Six Sigma and TQM?
The main difference in these two quality management tools lies in the fact that six sigma is focused on eliminating defects and total quality management (TQM), emphasizes improving processes and reducing costs.
Six Sigma is a methodology for continuous improvement. This approach emphasizes eliminating defects through statistical methods like control charts, Pareto analysis, and p-charts.
This method aims to reduce variation in product production. This is done by identifying and correcting the root causes of problems.
Total quality management refers to the monitoring and measurement of all aspects in an organization. It also includes the training of employees to improve performance.
It is often used to increase productivity.
What are the four main functions of management?
Management is responsible for planning, organizing, directing, and controlling people and resources. It includes the development of policies and procedures as well as setting goals.
Management assists an organization in achieving its goals by providing direction, coordination and control, leadership, motivation, supervision and training, as well as evaluation.
The following are the four core functions of management
Planning - Planning refers to deciding what is needed.
Organizing - Organization involves deciding what should be done.
Directing - Directing means getting people to follow instructions.
Controlling – This refers to ensuring that tasks are carried out according to plan.
What is Six Sigma?
It's a strategy for quality improvement that emphasizes customer care and continuous learning. The goal is to eliminate defects by using statistical techniques.
Motorola developed Six Sigma in 1986 to help improve its manufacturing processes.
It was quickly adopted by the industry and many companies are now using six-sigma to improve product design, production, delivery, customer service, and product design.
Statistics
- The BLS says that financial services jobs like banking are expected to grow 4% by 2030, about as fast as the national average. (wgu.edu)
- 100% of the courses are offered online, and no campus visits are required — a big time-saver for you. (online.uc.edu)
- The profession is expected to grow 7% by 2028, a bit faster than the national average. (wgu.edu)
- Hire the top business lawyers and save up to 60% on legal fees (upcounsel.com)
- Our program is 100% engineered for your success. (online.uc.edu)
External Links
How To
How can you implement the Kaizen technique?
Kaizen means continuous improvement. This term was first used by Toyota Motor Corporation in the 1950s. It refers to the Japanese philosophy that emphasizes continuous improvement through small incremental changes. It's a process where people work together to improve their processes continuously.
Kaizen, a Lean Manufacturing method, is one of its most powerful. The concept involves employees responsible for manufacturing identifying problems and trying to fix them before they become serious issues. This will increase the quality and decrease the cost of the products.
The main idea behind kaizen is to make every worker aware of what happens around him/her. Correct any errors immediately to avoid future problems. So, if someone notices a problem while working, he/she should report it to his/her manager.
When doing kaizen, there are some principles we must follow. Always start with the end product in mind and work our way back to the beginning. If we want to improve our factory for example, we start by fixing the machines that make the final product. We then fix the machines producing components, and the machines producing raw materials. We then fix the workers that work with those machines.
This is why it's called "kaizen" because it works step-by-step to improve everything. After we're done with the factory, it's time to go back and fix the problem.
Before you can implement kaizen into your business, it is necessary to learn how to measure its effectiveness. There are many methods to assess if kaizen works well. One of these ways is to check the number of defects found on the finished products. Another way is determining how much productivity increased after implementing kaizen.
To determine if kaizen is effective, you should ask yourself why you chose to implement kaizen. Was it just because it was the law or because you wanted to save money? Did you really believe that it would be a success factor?
Congratulations if you answered "yes" to any of the questions. Now you're ready for kaizen.